Device and method for warm forming of metal and carbon fiber prepreg composite material components
A composite material component and carbon fiber prepreg technology, which is applied in the manufacturing field of metal and carbon fiber prepreg composite material components, and can solve the problems such as no processing of heterogeneous composite material components, no obvious advantages in light weight, and complicated process. , to prevent premature breakage, overcome the large forming resistance, and ensure the effect of mechanical properties
- Summary
- Abstract
- Description
- Claims
- Application Information
AI Technical Summary
Problems solved by technology
Method used
Image
Examples
Embodiment Construction
[0022] see figure 1 , the warm forming device of the metal and carbon fiber prepreg composite material component of the present invention has an upper mold part and a lower mold part, and the upper mold part and the lower mold part constitute a stamping forming unit. Wherein, the upper mold part includes an upper mold fixed plate 44 , a mold handle 45 , and a die 10 . The lower surface of the die 10 is a binder surface, and a downwardly protruding calendering bead 46 is arranged on the binder surface. The top of the die 10 is fixedly connected to the upper mold fixed plate 44, and the upper mold fixed plate 44 is fixedly connected to the die handle 45, and the die handle 45 is connected to the press slide block ( figure 1 omitting the press slider) to be connected, and the press drives the mold handle 45 and the upper mold fixing plate 44 to move vertically up and down, thereby driving the die 10 to move vertically up and down.
[0023]The lower mold part is directly below t...
PUM
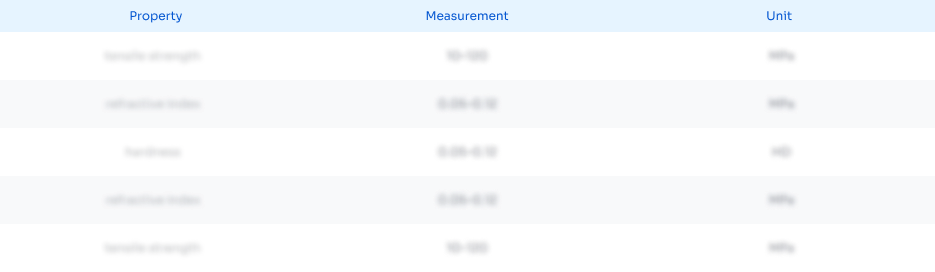
Abstract
Description
Claims
Application Information

- Generate Ideas
- Intellectual Property
- Life Sciences
- Materials
- Tech Scout
- Unparalleled Data Quality
- Higher Quality Content
- 60% Fewer Hallucinations
Browse by: Latest US Patents, China's latest patents, Technical Efficacy Thesaurus, Application Domain, Technology Topic, Popular Technical Reports.
© 2025 PatSnap. All rights reserved.Legal|Privacy policy|Modern Slavery Act Transparency Statement|Sitemap|About US| Contact US: help@patsnap.com