Processing process for single handle
A processing technology and handle technology, which is applied in the field of single handle processing technology, can solve the problems of uneven handle material, short service life, low handle quality, etc., and achieve a harmonious and beautiful product appearance, reduce production costs, and save processing materials. Effect
- Summary
- Abstract
- Description
- Claims
- Application Information
AI Technical Summary
Problems solved by technology
Method used
Examples
Embodiment 1
[0020] A processing technology for a single handle, comprising the following steps:
[0021] (1) The counterweight is produced through the counterweight mold. The outer diameter of the counterweight is Φ41.8mm, and the inner diameter of the counterweight is Φ16.5mm. After mixing white oil and water in a ratio of 1:4, put Soak the counterweight in the mixed solution for 15 minutes, then take out the counterweight and put it on the sieve to dry until the surface is dry. Finally, wipe the surface of the counterweight with a clean rag, and then blow the entire surface of the counterweight with an air gun Store it in a dustproof box for later use;
[0022] (2) Take a plastic inner sleeve mold with an inner diameter of Φ16.6mm and install it on the injection molding machine equipment, and at the same time insert a M5*5mm copper nut into the plastic inner sleeve mold, and place the copper nut on the core of the plastic inner sleeve mold. The steps of the parts are tightly attached t...
Embodiment 2
[0028] A processing technology for a single handle, comprising the following steps:
[0029] (1) The counterweight is produced through the counterweight mold. The outer diameter of the counterweight is Φ46.5mm, and the inner diameter of the counterweight is Φ18.5mm. After mixing white oil and water in a ratio of 1:4, put Soak the counterweight in the mixed solution for 15 minutes, then take out the counterweight and put it on the sieve to dry until the surface is dry. Finally, wipe the surface of the counterweight with a clean rag, and then blow the entire surface of the counterweight with an air gun Store it in a dustproof box for later use;
[0030] (2) Take a plastic inner sleeve mold with an inner diameter of Φ18.6mm and install it on the injection molding machine equipment, and at the same time insert a M5*5mm copper nut into the plastic inner sleeve mold, and place the copper nut on the core of the plastic inner sleeve mold. The steps of the parts are tightly attached t...
PUM
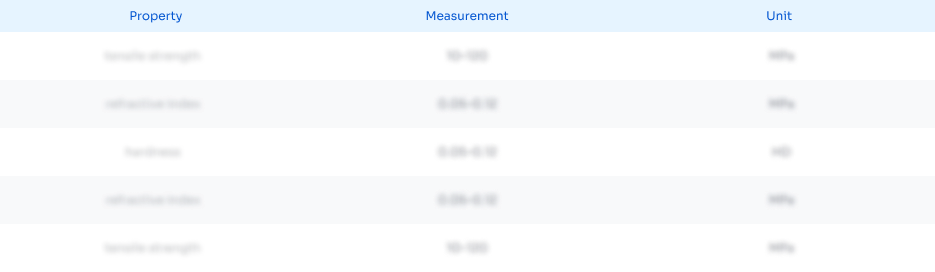
Abstract
Description
Claims
Application Information

- R&D Engineer
- R&D Manager
- IP Professional
- Industry Leading Data Capabilities
- Powerful AI technology
- Patent DNA Extraction
Browse by: Latest US Patents, China's latest patents, Technical Efficacy Thesaurus, Application Domain, Technology Topic, Popular Technical Reports.
© 2024 PatSnap. All rights reserved.Legal|Privacy policy|Modern Slavery Act Transparency Statement|Sitemap|About US| Contact US: help@patsnap.com