Air well technological testing system during full life cycle
A technology of full life cycle and process test, applied in the field of process test system of gas well life cycle, which can solve the problems of verification, low flowback rate, and inability to realize parameters, etc.
- Summary
- Abstract
- Description
- Claims
- Application Information
AI Technical Summary
Problems solved by technology
Method used
Image
Examples
Embodiment 1
[0018] Such as figure 1 and figure 2 As shown, a gas well life cycle process test system includes an air compressor 101, a water tank 102, a gas storage well 103, a plunger pump 104, a gas-liquid mixing precise control injection system 105, an input manifold 106, and a process test well 107 , throttling manifold 108, automatic separation and metering system 109, noise reduction and filtration recycling system 110, sewage collection 111, downhole multi-point parameter direct reading test interpretation system 2 and visual monitoring operation integration system 3, the air compressor 101 is connected to The gas storage well 103 and the water tank 102 are connected to the plunger pump 104, the gas storage well 103 and the plunger pump 104 are connected to the gas-liquid mixing precise control injection system 105, the gas-liquid mixing precise control injection system 105, the input manifold 106, the process test well 107, Throttle manifold 108, automatic separation and meterin...
Embodiment 2
[0021] Such as figure 1 As shown, on the basis of Example 1, the gas-liquid mixing accurately controls the working pressure of the injection system 105 to 70MPa, the injection flow rate is 0-720m3 / d, the gas volume is 1000-100000N m3 / d, and the mixing ratio is the liquid volume 0-100%, air volume 0-100%, measurement accuracy is 0.5% liquid volume, 1% air volume. It is conducive to carrying out theoretical research, tool performance evaluation and process simulation experiments under close working conditions, and can shorten the development process of processes, tools and equipment. When the gas-liquid mixing precise control injection system 105 is used in test well tests, the two phases of gas and liquid are precisely prepared and mixed according to different proportions, and injected into the process test well; the gas-liquid mixing precise control injection system 105 is controlled by the gas pipeline , infusion manifold, gas-liquid mixing device, control valves and sensors...
Embodiment 3
[0023] Such as figure 1 As shown, on the basis of Example 1-2, the process test well 107 is a double-casing high-inclination process test well, the working pressure is 70Mpa, the wellbore is a high-inclination well, the well depth is 1700m, and the vertical well section is 1200m The inclined well section is 500m long, the vertical well depth is 1500m, and the inclination is 80°. Casing cementing, after passing the pressure test, the 51 / 2" construction casing and 27 / 8" operation tubing are run in. The wellhead adopts KQ78 / 65-7011 valve wellhead, and the input manifold controls from 73 / 4 "Large annulus gas injection, choke manifold controls 51 / 2" casing small annulus and the return gas-liquid mixture in the working tubing; Gas, the throttling manifold controls the return of the gas-liquid mixture from the 73 / 4" large annulus; or others.
[0024] The working pressure of the gas storage well 103 and the plunger pump 104 is 70Mpa. The working pressure of the gas storage well 103...
PUM
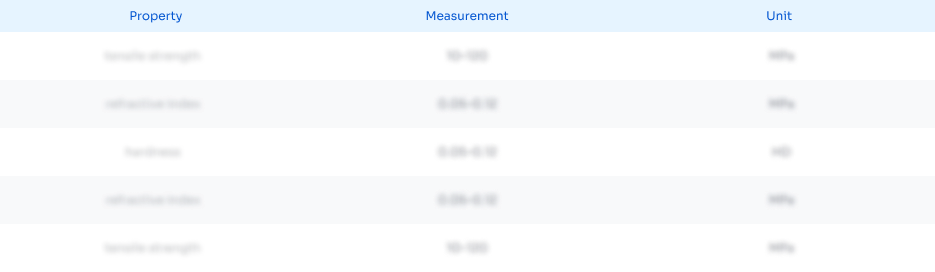
Abstract
Description
Claims
Application Information

- R&D
- Intellectual Property
- Life Sciences
- Materials
- Tech Scout
- Unparalleled Data Quality
- Higher Quality Content
- 60% Fewer Hallucinations
Browse by: Latest US Patents, China's latest patents, Technical Efficacy Thesaurus, Application Domain, Technology Topic, Popular Technical Reports.
© 2025 PatSnap. All rights reserved.Legal|Privacy policy|Modern Slavery Act Transparency Statement|Sitemap|About US| Contact US: help@patsnap.com