Lightweight noise-reducing semi-aromatic nylon material and preparation method and application thereof
A semi-aromatic nylon and noise reduction technology, applied in the field of semi-aromatic nylon materials and their preparation, can solve the problems of high density and increase the weight of the final product, and achieve the effects of uniform distribution, light weight and good mechanical properties
- Summary
- Abstract
- Description
- Claims
- Application Information
AI Technical Summary
Problems solved by technology
Method used
Image
Examples
preparation example Construction
[0045]
[0046] A kind of preparation method of lightweight noise-reducing semi-aromatic nylon material, it comprises the steps:
[0047] (1) Mix 60-70 parts of dry semi-aromatic nylon, 0.2-0.5 parts of lubricant, 0.5-1 part of antioxidant, and 0.5-1 part of coupling agent to obtain a premix;
[0048](2) Add the premixed material from the main feeding port of the twin-screw extruder, add 10-20 parts of dry glass microspheres from the first side feeding port of the twin-screw extruder, add 10-30 parts A portion of dry glass fiber is fed from the second side feed port of the twin-screw extruder, melted and extruded and granulated by the twin-screw extruder to obtain a light-weight, noise-reducing semi-aromatic nylon material.
[0049] Wherein, in the step (1), the above-mentioned dried semi-aromatic nylon is obtained by drying the semi-aromatic nylon in a drying oven at 100-120°C for 8-10 hours, and the drying temperature may preferably be 110°C.
[0050] In step (1), the abo...
Embodiment 1
[0064] The content of each component of the lightweight noise-reducing semi-aromatic nylon material of this embodiment is shown in Table 1 below.
[0065] Table 1 The component content table of the lightweight noise-reducing semi-aromatic nylon material of Example 1
[0066]
[0067]
[0068] In Table 1, the parts by weight of semi-aromatic nylon, glass microspheres and glass fibers are the weight after drying (dry weight), the same below.
[0069] The preparation method of the lightweight noise-reducing semi-aromatic nylon material in the present embodiment comprises the steps:
[0070] (1), dry semi-aromatic nylon in a drying oven at 110°C for 8 hours to obtain dry semi-aromatic nylon; dry the glass beads in a drying oven at 90°C for 2 hours to obtain dried glass beads; Dry the fibers in a drying oven at 90°C for 2 hours to obtain dried glass fibers;
[0071] (2), according to the weight part of Table 1, take dry semi-aromatic nylon, lubricant, antioxidant, coupling ...
Embodiment 2
[0076] The content of each component of the lightweight noise-reducing semi-aromatic nylon material of this embodiment is shown in Table 2 below.
[0077] Table 2 The component content table of the lightweight noise-reducing semi-aromatic nylon material of embodiment two
[0078]
[0079] The preparation method of the lightweight noise-reducing semi-aromatic nylon material in the present embodiment comprises the steps:
[0080] (1), dry semi-aromatic nylon in a drying oven at 110°C for 8 hours to obtain dry semi-aromatic nylon; dry the glass beads in a drying oven at 90°C for 2 hours to obtain dried glass beads; Dry the fibers in a drying oven at 90°C for 2 hours to obtain dried glass fibers;
[0081] (2), according to the weight part of Table 2, take dry semi-aromatic nylon, lubricant, antioxidant, coupling agent and mix uniformly, obtain premix;
[0082] (3) Add the premixed material from the main feed port of the twin-screw extruder, add the dry glass beads from the fi...
PUM
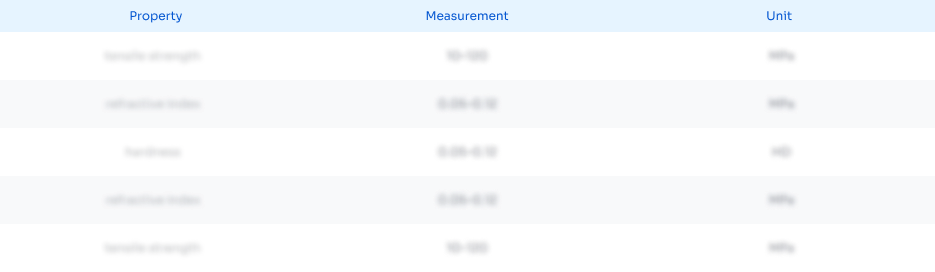
Abstract
Description
Claims
Application Information

- R&D
- Intellectual Property
- Life Sciences
- Materials
- Tech Scout
- Unparalleled Data Quality
- Higher Quality Content
- 60% Fewer Hallucinations
Browse by: Latest US Patents, China's latest patents, Technical Efficacy Thesaurus, Application Domain, Technology Topic, Popular Technical Reports.
© 2025 PatSnap. All rights reserved.Legal|Privacy policy|Modern Slavery Act Transparency Statement|Sitemap|About US| Contact US: help@patsnap.com