Method and device for detecting radial runout of lathe spindle in machining state
A lathe spindle and radial runout technology, which is applied to metal processing equipment, metal processing machine parts, manufacturing tools, etc., can solve problems such as inability to measure radial runouts, and achieve the effects of small space limitations, high measurement efficiency, and obvious advantages
- Summary
- Abstract
- Description
- Claims
- Application Information
AI Technical Summary
Problems solved by technology
Method used
Image
Examples
Embodiment Construction
[0027] The present invention will be further described below in conjunction with the accompanying drawings. In order to ensure the smooth implementation of the method, there must be a mandrel holding part and a dynamic testing part.
[0028] figure 1 As shown in the schematic diagram of the structure of the mandrel holding part, after the tail of the processed round rod 1 is pre-processed to have the same diameter as the inner hole of the installation sleeve 2, the installation sleeve 2 is fixedly connected to the processed round rod 1 through the set screw 3; the connection sleeve 4 Use non-magnetic materials, and the installation sleeve 2 is fixedly connected with the installation screw 5; the strong magnet 6 is placed in the inner hole of the installation sleeve 2, and the strong magnet 6 and the tempered glass 8 are pressed together by the clamp cover 7 with internal threads , finally, the tested mandrel 9 can be attracted to the smooth surface of the tempered glass 8 . ...
PUM
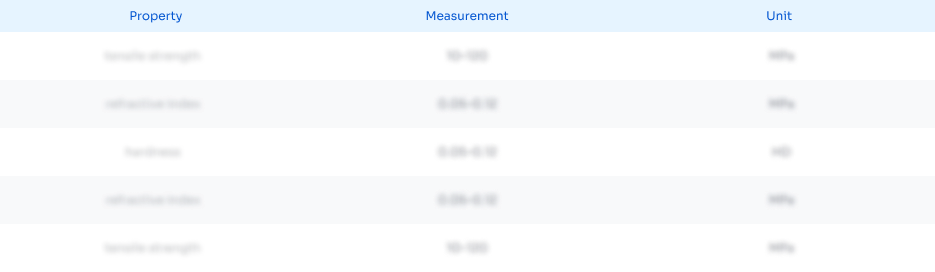
Abstract
Description
Claims
Application Information

- R&D
- Intellectual Property
- Life Sciences
- Materials
- Tech Scout
- Unparalleled Data Quality
- Higher Quality Content
- 60% Fewer Hallucinations
Browse by: Latest US Patents, China's latest patents, Technical Efficacy Thesaurus, Application Domain, Technology Topic, Popular Technical Reports.
© 2025 PatSnap. All rights reserved.Legal|Privacy policy|Modern Slavery Act Transparency Statement|Sitemap|About US| Contact US: help@patsnap.com