Mechanical alloying preparation method for niobium-silicon powder
A technology of mechanical alloying and niobium silicon powder, which is applied in the field of material processing, can solve the problems of small production output, uneven particle size distribution of powder materials, and expensive equipment, so as to optimize the alloying effect, improve the uniformity of components, Effect of inhibiting oxidation phenomenon
- Summary
- Abstract
- Description
- Claims
- Application Information
AI Technical Summary
Problems solved by technology
Method used
Examples
Embodiment Construction
[0015] The present invention will be further described below in combination with specific embodiments.
[0016] The preparation method of mechanical alloying of niobium silicon powder includes the following steps, the selected alloy components include Al: 12-14%, Cr: 1-1.6%, V: 0.2-0.5%, and the balance is Nb,
[0017] Select the element powder corresponding to the above components according to the above atomic percentage, the particle size of the powder is 150-200 microns, and then add it to the ethylene glycol solvent to obtain the mixture, the quality of the ethylene glycol solvent is 4% of the total mass of the element powder times, followed by ultrasonic vibration stirring, stirring for 10 minutes and then heating and concentrating the above solvent under the condition of continuing to stir, concentrating ethylene glycol to 0.8 times the total mass of the element powder. Stir mechanically with a rotating shaft. The above process is to make all the elemental powders can b...
PUM
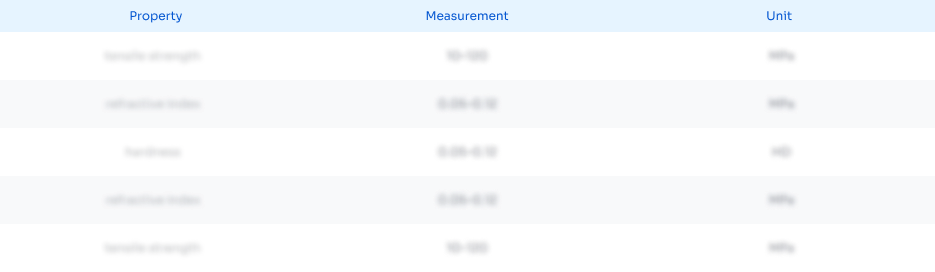
Abstract
Description
Claims
Application Information

- Generate Ideas
- Intellectual Property
- Life Sciences
- Materials
- Tech Scout
- Unparalleled Data Quality
- Higher Quality Content
- 60% Fewer Hallucinations
Browse by: Latest US Patents, China's latest patents, Technical Efficacy Thesaurus, Application Domain, Technology Topic, Popular Technical Reports.
© 2025 PatSnap. All rights reserved.Legal|Privacy policy|Modern Slavery Act Transparency Statement|Sitemap|About US| Contact US: help@patsnap.com