Preparation method of wear-resistant steel plate
A wear-resistant steel plate and material mixing technology, which is applied in the field of wear-resistant steel plate preparation, can solve problems such as part failure, reduce the surface contact fatigue strength of the protective steel plate, and compete with sintered protective steel plate, and achieve high overall density and surface density and glossiness Good, the effect of high product performance indicators
- Summary
- Abstract
- Description
- Claims
- Application Information
AI Technical Summary
Problems solved by technology
Method used
Examples
Embodiment Construction
[0009] The present invention will be further described in conjunction with examples.
[0010] A method for preparing a wear-resistant steel plate, comprising the following steps:
[0011] 1) Mixing, powder material composition by weight percentage: C:0.03~0.10%, Si:0.10~0.50%, Mn:1.00~1.80%, Ti:0.010~0.030%, Nb:0.02~0.09%, Cu: 0.10~0.50%, the balance is iron; then grind it into a powder with an average particle size of no more than 100 microns, and use multiple filling methods to press in the mold with a pressure of 500-550MPa for 10-60 minutes to form;
[0012] 2) Sintering, first pre-sintering at 650-700°C for 1-2 hours, then shaping in the mold under a pressure of 180-200MPa, and then sintering at 1000-1150°C and holding for 1-1.5 hours to obtain continuous billet;
[0013] 3) Heating the continuous casting slab to 1050-1250°C; rolling 3-20 passes at the recrystallization temperature of the steel in the range of 900-1150°C to refine the austenite grains, improve the quali...
PUM
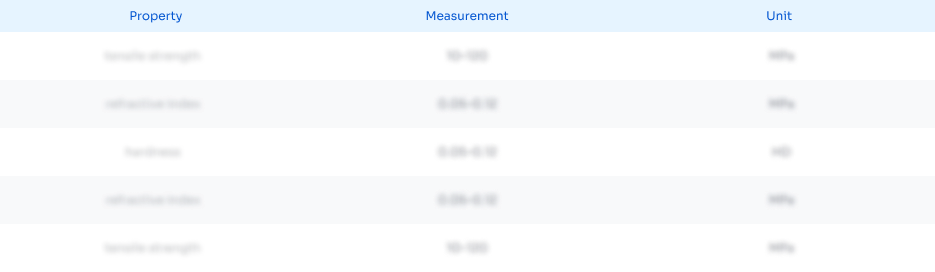
Abstract
Description
Claims
Application Information

- R&D
- Intellectual Property
- Life Sciences
- Materials
- Tech Scout
- Unparalleled Data Quality
- Higher Quality Content
- 60% Fewer Hallucinations
Browse by: Latest US Patents, China's latest patents, Technical Efficacy Thesaurus, Application Domain, Technology Topic, Popular Technical Reports.
© 2025 PatSnap. All rights reserved.Legal|Privacy policy|Modern Slavery Act Transparency Statement|Sitemap|About US| Contact US: help@patsnap.com