Precision casting molding process
A molding process and precision casting technology, applied in casting molding equipment, casting molds, casting mold components, etc., can solve the problems of complex wax mold process, difficult repair welding and grinding of the central part of castings, etc., to reduce production costs, dimensional stability, The effect of small form and position error
- Summary
- Abstract
- Description
- Claims
- Application Information
AI Technical Summary
Problems solved by technology
Method used
Examples
Embodiment
[0013] In the precision casting molding process of this embodiment, the molding process steps are as follows: (1) Put the wax material into the mixer, heat it to 45-48°C, and stir it into a paste; (2) Make the two metal pillar molds respectively by flexible Insert the two die sleeve holes of the mold sleeve into the flexible mold sleeve, and place the three in the mold cavity of the metal mold, and then make it close the upper and lower molds; (3) mix the paste wax with 3.5 Atmospheric pressure is injected into the mould, and the casting body wax mold and the sprue wax mold are poured respectively, and cooled at room temperature for 30-60 minutes; (4) Open the upper and lower molds of the metal mold, and put the two metal columns in it The mold is pulled out, the casting body wax mold and the sprue wax mold are demoulded, put them in the pool to cool to 22-27°C, and take them out for use; (5) The casting body wax mold made in step (4) is trimmed, and then used A hot knife at 1...
PUM
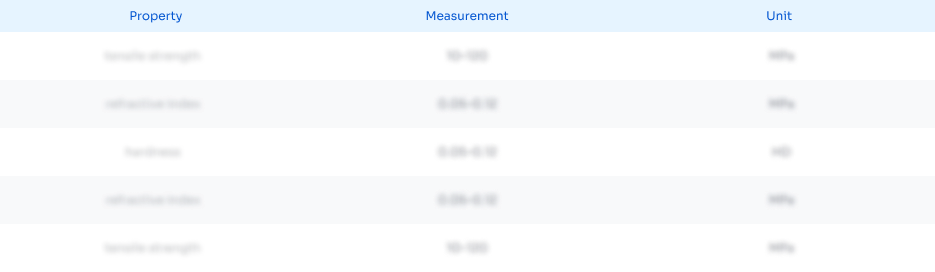
Abstract
Description
Claims
Application Information

- R&D Engineer
- R&D Manager
- IP Professional
- Industry Leading Data Capabilities
- Powerful AI technology
- Patent DNA Extraction
Browse by: Latest US Patents, China's latest patents, Technical Efficacy Thesaurus, Application Domain, Technology Topic, Popular Technical Reports.
© 2024 PatSnap. All rights reserved.Legal|Privacy policy|Modern Slavery Act Transparency Statement|Sitemap|About US| Contact US: help@patsnap.com