An Electromagnetic Progressive Flexible Composite Forming Method
A composite forming and electromagnetic forming technology, applied in the field of parts forming and manufacturing, can solve the problems of difficult forming of large and difficult-to-deform parts, reduce the manufacturing cost of large molds, and shorten the production cycle, so as to shorten the production cycle, improve plastic deformation ability and forming accuracy , Solve the effect of difficult forming
- Summary
- Abstract
- Description
- Claims
- Application Information
AI Technical Summary
Problems solved by technology
Method used
Image
Examples
Embodiment Construction
[0026] In order to make the object, technical solution and advantages of the present invention clearer, the present invention will be further described in detail below in conjunction with the accompanying drawings and embodiments. It should be understood that the specific embodiments described here are only used to explain the present invention, not to limit the present invention. In addition, the technical features involved in the various embodiments of the present invention described below can be combined with each other as long as they do not constitute a conflict with each other.
[0027] see Figure 1 to Figure 4 , The electromagnetic progressive flexible composite forming method provided by the preferred embodiment of the present invention, the electromagnetic progressive flexible composite forming method combines electromagnetic progressive forming with a flexible multi-point mold, which is suitable for the overall uniform forming of large and difficult-to-deform shell ...
PUM
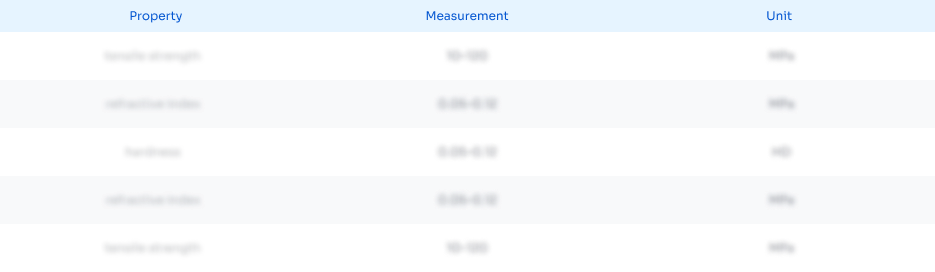
Abstract
Description
Claims
Application Information

- R&D
- Intellectual Property
- Life Sciences
- Materials
- Tech Scout
- Unparalleled Data Quality
- Higher Quality Content
- 60% Fewer Hallucinations
Browse by: Latest US Patents, China's latest patents, Technical Efficacy Thesaurus, Application Domain, Technology Topic, Popular Technical Reports.
© 2025 PatSnap. All rights reserved.Legal|Privacy policy|Modern Slavery Act Transparency Statement|Sitemap|About US| Contact US: help@patsnap.com