Energy-saving heat exchanger for production of foamed plastic
An energy-saving heat exchanger and foam plastic technology, applied in the field of foam plastic production, can solve the problems of poor foaming effect of EPS raw material particles, rough surface of foam plastic products, lowering the temperature of foam plastic molds, etc., so as to avoid heat volatilization in vain, The effect of shortening working time and reducing heat
- Summary
- Abstract
- Description
- Claims
- Application Information
AI Technical Summary
Problems solved by technology
Method used
Image
Examples
Embodiment Construction
[0016] In order to facilitate the understanding of those skilled in the art, the present invention will be further described below in conjunction with the accompanying drawings.
[0017] figure 2 It is a schematic diagram of the overall structure of the present invention, comprising a foam particle warehouse 2, a foam plastic mold 6, a high-temperature steam tank 3 and a cooling pool 7, and an air duct 4 is provided between the foam particle warehouse 2 and the foam plastic mold 6 to connect, and the high-temperature steam tank 3 Pipelines are provided between the foam plastic mold 6 to connect, the cooling pool 7 and the foam plastic mold 6 are respectively provided with water inlet pipes 9 and water outlet pipes 5 to connect, and part of the air pipes 4 are located in the cooling pool 7; the ends of the air pipes 4 A fan 1 is provided; a cooling tower 8 is provided in the cooling pool 7; a water pump 10 is provided on the water inlet pipe 9.
[0018] Concrete mode of work ...
PUM
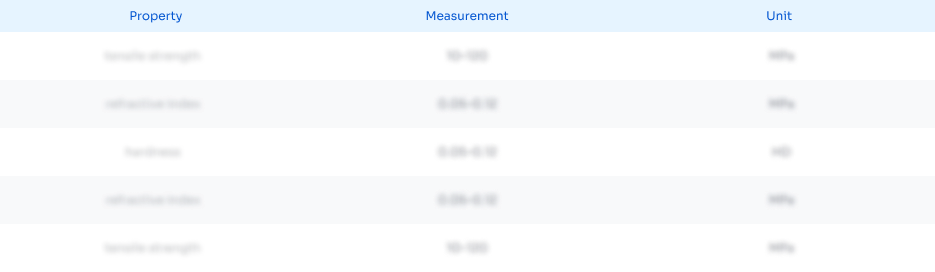
Abstract
Description
Claims
Application Information

- R&D Engineer
- R&D Manager
- IP Professional
- Industry Leading Data Capabilities
- Powerful AI technology
- Patent DNA Extraction
Browse by: Latest US Patents, China's latest patents, Technical Efficacy Thesaurus, Application Domain, Technology Topic, Popular Technical Reports.
© 2024 PatSnap. All rights reserved.Legal|Privacy policy|Modern Slavery Act Transparency Statement|Sitemap|About US| Contact US: help@patsnap.com