Connector for carbon-fiber composite-core optical-fiber wires
A technology of wire connectors and composite cores, applied in light guides, optics, instruments, etc., can solve problems such as fiber shedding, achieve the effects of increasing the contact area, improving fastening performance, and avoiding bending
- Summary
- Abstract
- Description
- Claims
- Application Information
AI Technical Summary
Problems solved by technology
Method used
Image
Examples
Embodiment 1
[0030] Such as Figure 1 to Figure 3 As shown, the present invention includes an outer crimping pipe 1, which is an integrally formed hollow pipe, and the outer crimping pipe 1 is provided with a first inner lining pipe 2, a first wedge-shaped clamp support 3, and a connecting rod in sequence from left to right. The pipe 4, the second wedge-shaped clamp support 5 and the second liner pipe 6, the first wedge-shaped clamp support 3 and the second wedge-shaped clamp support 5 are all provided with matching wedge-shaped clamps 7, and the front end surface of the connecting pipe 3 is opened Operation hole 9, the operation hole 9 is oval, the operation hole 9 is provided with a sealing cover 10, the inner wall of the connecting pipe 4 is coated with a rubber coating (not shown), and its inner wall is smooth.
[0031] When this structure is in use, the operation hole 9 is easy to improve the work efficiency in the process of welding the inner cores of two optical fiber wires. During ...
Embodiment 3
[0037] A splicing method based on the carbon fiber composite core optical fiber lead splice in embodiment 2, comprising the following steps:
[0038] Step 1: Strip the insulation layer and protective layer of the two optical fiber wires to expose the inner core of the optical fiber in the inner layer;
[0039] Step 2: Pass one of the optical fiber wires through the outer crimping tube, and then pass the free end of the inner core of the left optical fiber through the first inner lining tube and the wedge-shaped clip to make it protrude from the connecting tube and out of the operation hole, and insert the right side The free end of the optical fiber inner core passes through the second inner liner and the wedge-shaped clamp respectively to make it protrude from the connection tube and out of the operation hole. In the clamp, the unstripped part of the right fiber optic wire is located in the second inner liner and the wedge-shaped clamp on the right, and the free ends of the t...
PUM
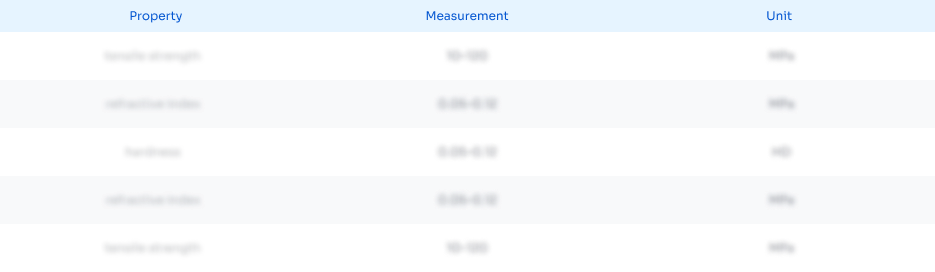
Abstract
Description
Claims
Application Information

- Generate Ideas
- Intellectual Property
- Life Sciences
- Materials
- Tech Scout
- Unparalleled Data Quality
- Higher Quality Content
- 60% Fewer Hallucinations
Browse by: Latest US Patents, China's latest patents, Technical Efficacy Thesaurus, Application Domain, Technology Topic, Popular Technical Reports.
© 2025 PatSnap. All rights reserved.Legal|Privacy policy|Modern Slavery Act Transparency Statement|Sitemap|About US| Contact US: help@patsnap.com