Tensile fatigue-four-point flexural fatigue in-situ mechanical testing device and testing method thereof
A four-point bending and testing device technology, applied in the direction of using a stable bending force to test the strength of materials, measuring devices, and using repeated force/pulse force to test the strength of materials, etc. Real-time observation of material microstructure and other problems, to achieve the effect of compact structure and small volume
- Summary
- Abstract
- Description
- Claims
- Application Information
AI Technical Summary
Problems solved by technology
Method used
Image
Examples
Embodiment Construction
[0040] The detailed content of the present invention and its specific implementation will be further described below in conjunction with the accompanying drawings.
[0041] see Figure 1 to Figure 6 As shown, the tensile fatigue-four-point bending fatigue in-situ mechanical testing device of the present invention includes four-point bending preload loading and detection unit, four-point bending fatigue loading unit, tensile preload loading and detection unit, tensile fatigue Load unit.
[0042] The four-point bending preload loading unit is: the DC servo motor I1 is connected to the test platform base 33 through the motor flange I2, and the deceleration and torque increase are realized through the worm gear I5 and the worm I6, driving the one-way ball screw II36 to The rotary motion is converted into the linear reciprocating motion of the bending module support seat 34 , finally realizing the quasi-static loading of the four-point bending test indenter 28 on the tested sample...
PUM
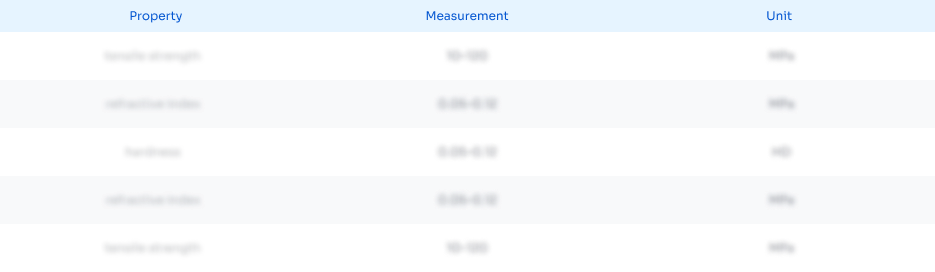
Abstract
Description
Claims
Application Information

- R&D
- Intellectual Property
- Life Sciences
- Materials
- Tech Scout
- Unparalleled Data Quality
- Higher Quality Content
- 60% Fewer Hallucinations
Browse by: Latest US Patents, China's latest patents, Technical Efficacy Thesaurus, Application Domain, Technology Topic, Popular Technical Reports.
© 2025 PatSnap. All rights reserved.Legal|Privacy policy|Modern Slavery Act Transparency Statement|Sitemap|About US| Contact US: help@patsnap.com