A Feedback Control Vibration Table Based on Stepping Motor
A technology of stepping motor and feedback control, which is applied in vibration testing, testing of machines/structural components, measuring devices, etc. It can solve the problems of complex structure of air-floating guide rails, high manufacturing precision requirements, and large space occupation, so as to reduce transportation costs. The effect of cost and transportation risk, low environmental humidity and dust requirements, easy to carry and place
- Summary
- Abstract
- Description
- Claims
- Application Information
AI Technical Summary
Problems solved by technology
Method used
Image
Examples
Embodiment Construction
[0024] The technical solutions in the embodiments of the present invention will be clearly and completely described below in conjunction with the accompanying drawings in the embodiments of the present invention. Obviously, the described embodiments are only part of the embodiments of the present invention, not all of them. Based on the embodiments of the present invention, all other embodiments obtained by persons of ordinary skill in the art without making creative efforts belong to the protection scope of the present invention.
[0025] Such as figure 1 As shown, it is a three-dimensional structure diagram of the vibration table based on the feedback control of the stepping motor of the present invention, which is mainly composed of two parts such as the vibration table body 1 and the controller 24 . Wherein, the control system in the controller 24 is used to generate a pulse waveform to control the vibration of the motor, and to receive the speed information fed back by th...
PUM
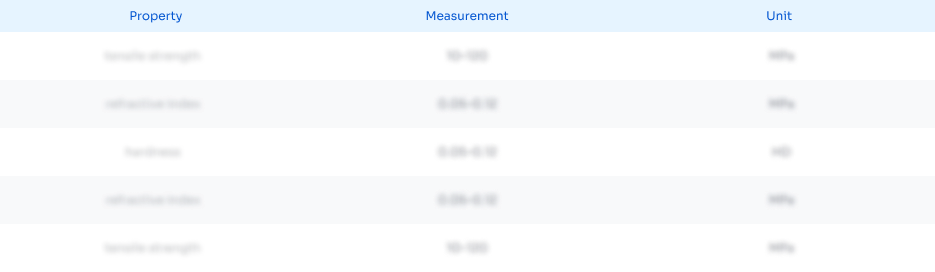
Abstract
Description
Claims
Application Information

- R&D
- Intellectual Property
- Life Sciences
- Materials
- Tech Scout
- Unparalleled Data Quality
- Higher Quality Content
- 60% Fewer Hallucinations
Browse by: Latest US Patents, China's latest patents, Technical Efficacy Thesaurus, Application Domain, Technology Topic, Popular Technical Reports.
© 2025 PatSnap. All rights reserved.Legal|Privacy policy|Modern Slavery Act Transparency Statement|Sitemap|About US| Contact US: help@patsnap.com