Compound additive for textile sizing, and preparation method thereof
A composite auxiliary agent and textile technology, which is applied in the field of textile sizing composite auxiliary agent and its preparation, can solve problems such as poor use effect, low technological content, and lack of environmental protection performance, and achieve strong practicability, increase sizing rate, and raw material cheap effect
- Summary
- Abstract
- Description
- Claims
- Application Information
AI Technical Summary
Problems solved by technology
Method used
Examples
Embodiment 1
[0022] (1) Accurately weigh 40 parts of ethylene glycol salicylate, 38 parts of fatty alcohol polyoxyethylene ether, 32 parts of polyvinylpyrrolidone, 20 parts of dioctyl sodium sulfosuccinate, and sorrel 15 parts of alcohol ester, 12 parts of sodium sulfite, 8 parts of dimethyl azobisisobutyrate, 6 parts of quinol dimethacrylate, 8 parts of cocamidopropyl betaine, 6 parts of sulfonated lignin, carrageenan 4 parts, 2 parts of zinc phenolsulfonate, 2 parts of aluminum hydroxide, 3 parts of palmitic acid, 3 parts of methylenebisacrylamide, 100 parts of deionized water;
[0023] (2) Add dimethyl azobisisobutyrate, quinol dimethacrylate, sulfonated lignin, carrageenan, zinc phenolsulfonate, and aluminum hydroxide into the ball mill, mill for 1 hour, and then pour The mixture was added deionized water, and stirred for 2 hours at a stirring rate of 1000 rpm to obtain a preliminary mixed solution;
[0024] (3) Send the preliminary mixture into the reaction kettle, add ethylene glyco...
Embodiment 2
[0028] (1) Accurately weigh 43 parts of ethylene glycol salicylate, 40 parts of fatty alcohol polyoxyethylene ether, 34 parts of polyvinylpyrrolidone, 23 parts of dioctyl sodium sulfosuccinate, and sorrel 18 parts of alcohol ester, 14 parts of sodium sulfite, 10 parts of dimethyl azobisisobutyrate, 8 parts of quinol dimethacrylate, 9 parts of cocamidopropyl betaine, 7 parts of sulfonated lignin, carrageenan 5 parts, 3 parts of zinc phenolsulfonate, 3 parts of aluminum hydroxide, 4 parts of citric acid, 4 parts of polyethylene glycol dimethacrylate, 100 parts of deionized water;
[0029] (2) Add dimethyl azobisisobutyrate, quinol dimethacrylate, sulfonated lignin, carrageenan, zinc phenolsulfonate, and aluminum hydroxide into the ball mill, mill for 1.5 hours, and then pour The mixture was added deionized water, stirred at a stirring rate of 1500 rpm for 2.5 hours to obtain a preliminary mixed solution;
[0030] (3) Send the preliminary mixture into the reaction kettle, add et...
Embodiment 3
[0034] (1) Accurately weigh 46 parts of ethylene glycol salicylate, 42 parts of fatty alcohol polyoxyethylene ether, 35 parts of polyvinylpyrrolidone, 26 parts of dioctyl sodium sulfosuccinate, and sorrel 21 parts of alcohol ester, 16 parts of sodium sulfite, 12 parts of dimethyl azobisisobutyrate, 10 parts of quinol dimethacrylate, 10 parts of cocamidopropyl betaine, 8 parts of sulfonated lignin, carrageenan 6 parts, 4 parts of zinc phenolsulfonate, 4 parts of aluminum hydroxide, 5 parts of linoleic acid, 5 parts of ethylene glycol diglycidyl ether, 100 parts of deionized water;
[0035] (2) Add dimethyl azobisisobutyrate, quinol dimethacrylate, sulfonated lignin, carrageenan, zinc phenolsulfonate, and aluminum hydroxide into the ball mill, mill for 2 hours, and then pour The mixture was added deionized water, and stirred for 3 hours at a stirring rate of 2000 rpm to obtain a preliminary mixed solution;
[0036] (3) Send the preliminary mixture into the reaction kettle, add ...
PUM
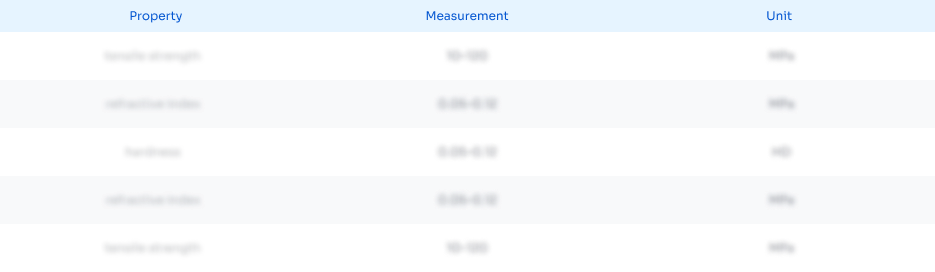
Abstract
Description
Claims
Application Information

- R&D
- Intellectual Property
- Life Sciences
- Materials
- Tech Scout
- Unparalleled Data Quality
- Higher Quality Content
- 60% Fewer Hallucinations
Browse by: Latest US Patents, China's latest patents, Technical Efficacy Thesaurus, Application Domain, Technology Topic, Popular Technical Reports.
© 2025 PatSnap. All rights reserved.Legal|Privacy policy|Modern Slavery Act Transparency Statement|Sitemap|About US| Contact US: help@patsnap.com