Hatch coaming with overall strength completely reckoned in and hatch longitudinal girder of bulk cargo ship
A technology for hatches and coamings, applied in the direction of hull decks, hulls, ship parts, etc., can solve problems that cannot be included in the overall longitudinal strength of hull girders, discontinuous structure types, and dangers of hatch coamings, and achieve weight reduction, Effects of improving fatigue life and increasing stiffness
- Summary
- Abstract
- Description
- Claims
- Application Information
AI Technical Summary
Problems solved by technology
Method used
Image
Examples
Embodiment approach
[0023] In further embodiments of the present invention, please continue to refer to figure 1 As shown, the longitudinal hatch coaming 1 forms an inverted trapezoidal groove 11 at the transverse bulkhead.
[0024] In a further embodiment of the present invention, since the longitudinal hatch coaming 1 is continuous along the ship's length direction, the longitudinal hatch coaming 1 is fully included in the total strength.
[0025] In a further embodiment of the present invention, the selection of the material of the longitudinal hatch coaming 1 and the main deck 2 according to the change of the elastic yield limit is illustrated. If the material of the main deck 2 is H36 steel, then the longitudinal hatch coaming 1 adopts H47 steel ; if the main deck 2 is made of H32 steel, the longitudinal hatch coaming 1 is made of H40 steel.
[0026] In a further embodiment of the present invention, the continuous feature of the longitudinal hatch coaming 1 also improves the shear resistanc...
PUM
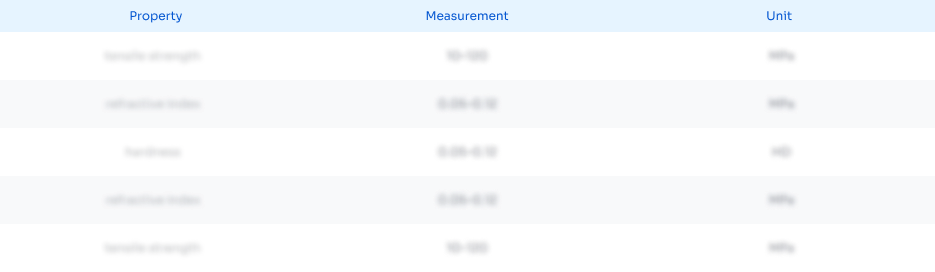
Abstract
Description
Claims
Application Information

- R&D Engineer
- R&D Manager
- IP Professional
- Industry Leading Data Capabilities
- Powerful AI technology
- Patent DNA Extraction
Browse by: Latest US Patents, China's latest patents, Technical Efficacy Thesaurus, Application Domain, Technology Topic, Popular Technical Reports.
© 2024 PatSnap. All rights reserved.Legal|Privacy policy|Modern Slavery Act Transparency Statement|Sitemap|About US| Contact US: help@patsnap.com