Servo stamping speed control method based on jerking movement degree
A technology of stamping speed and control method, applied in the field of stamping and forming, can solve problems such as lack of mathematical characteristics, and achieve the effects of reducing production noise, improving forming quality, and improving die life.
- Summary
- Abstract
- Description
- Claims
- Application Information
AI Technical Summary
Problems solved by technology
Method used
Image
Examples
Embodiment Construction
[0028] In order to make the object, technical solution and advantages of the present invention clearer, the present invention will be further described in detail below in conjunction with the accompanying drawings and embodiments. It should be understood that the specific embodiments described here are only used to explain the present invention, not to limit the present invention.
[0029] In a preferred embodiment of the present invention, a jerk-based servo stamping speed control method includes the following steps:
[0030] S1. Establish a three-dimensional model of the part to be stamped and import it into the finite element analysis software;
[0031] S2. Set material parameters, boundary conditions, contact conditions, and divide meshes;
[0032] S3, set the mathematical expression of the displacement amplitude curve as x=At 3 +Bt 2 +Ct+D, the mathematical expression of speed is v=3At 2 +2Bt+C, the mathematical expression of acceleration is a=6At+2B, and the mathemat...
PUM
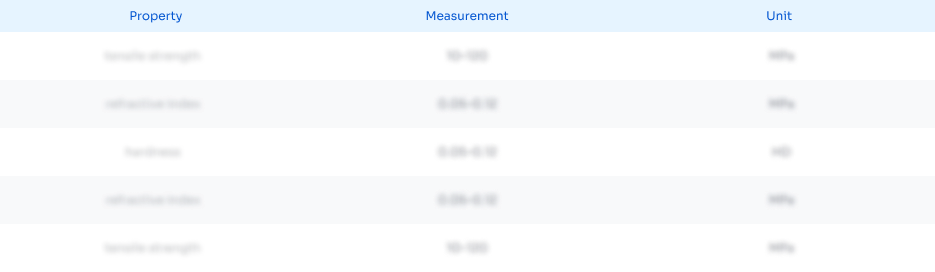
Abstract
Description
Claims
Application Information

- R&D
- Intellectual Property
- Life Sciences
- Materials
- Tech Scout
- Unparalleled Data Quality
- Higher Quality Content
- 60% Fewer Hallucinations
Browse by: Latest US Patents, China's latest patents, Technical Efficacy Thesaurus, Application Domain, Technology Topic, Popular Technical Reports.
© 2025 PatSnap. All rights reserved.Legal|Privacy policy|Modern Slavery Act Transparency Statement|Sitemap|About US| Contact US: help@patsnap.com