Hot die forging forming method for titanium material cartridge shape cover
A technology of medicine type cover and hot mold, applied in metal processing equipment and other directions, can solve the problems of difficult one-time forming, poor fluidity, large deformation, etc., and achieve the effect of being beneficial to forging, avoiding grain growth and dense organization.
- Summary
- Abstract
- Description
- Claims
- Application Information
AI Technical Summary
Problems solved by technology
Method used
Image
Examples
Embodiment 1
[0016] A hot die forging forming method for a titanium drug-type cover, comprising the following steps: ①Insulate the columnar blank at 890°C for 1 hour and apply a lubricant, and then put it into the preheated (650°C) prefabricated blank that has been applied with the lubricant. In the mold, the columnar blank pier is roughly formed into a preform on a hydraulic press; ②The preform is taken out of the prefabrication mold and placed in a preheated (650°C) final forging die that has been coated with lubricant, and forged on a hydraulic press to form a preform. Forgings of drug-masks; ③ Annealing treatment of forgings of drug-masks at 600°C for 0.5h. The grain size of the forging is 7, the elongation A(%)=29.5%, and the reduction of area Z(%)=70%.
Embodiment 2
[0018] A hot die forging forming method for a titanium drug-type cover, comprising the following steps: ①Insulate a columnar blank at 950°C for 1.5 hours and apply a lubricant, then put it into a preheated (750°C) mold that has been applied with a lubricant In the prefabricated mold, the columnar blank pier is roughly formed into a preform on a hydraulic press; ②The preform is taken out of the prefabricated mold and placed in a preheated (750°C) final forging die that has been coated with lubricant, and forged on a hydraulic press It becomes a drug-shape forging; ③The drug-shape forging is annealed at 500°C for 1h. The grain size of the forging is 6.5, the elongation A(%)=26.5%, and the reduction of area Z(%)=64%.
Embodiment 3
[0020] A hot die forging forming method for a titanium drug-type cover, comprising the following steps: ①Insulate the columnar blank at 850°C for 1 hour and apply a lubricant, then put it into the preheated (700°C) prefabricated blank that has been applied with the lubricant In the mold, the columnar billet pier is roughly formed into a preform on a hydraulic press; ②The preform is taken out of the prefabrication mold and placed in a preheated (700°C) final forging die that has been coated with lubricant, and forged on a hydraulic press to become Forgings of drug-masks; ③ Annealing treatment of forgings of drug-masks at 550°C for 0.5h. The grain size of the forging is 7, the elongation A(%)=28%, and the reduction of area Z(%)=69%.
PUM
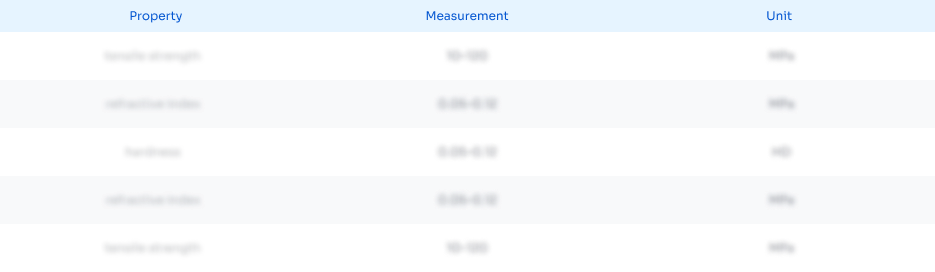
Abstract
Description
Claims
Application Information

- R&D
- Intellectual Property
- Life Sciences
- Materials
- Tech Scout
- Unparalleled Data Quality
- Higher Quality Content
- 60% Fewer Hallucinations
Browse by: Latest US Patents, China's latest patents, Technical Efficacy Thesaurus, Application Domain, Technology Topic, Popular Technical Reports.
© 2025 PatSnap. All rights reserved.Legal|Privacy policy|Modern Slavery Act Transparency Statement|Sitemap|About US| Contact US: help@patsnap.com