Compound additive for limestone-gypsum wet-process flue gas desulfurization
A wet flue gas desulfurization and compound additive technology, applied in gas treatment, separation methods, chemical instruments and methods, etc., can solve the problems of delayed onset time, short duration, long duration, etc., and achieve long duration , fast onset, prolonged effect
- Summary
- Abstract
- Description
- Claims
- Application Information
AI Technical Summary
Problems solved by technology
Method used
Image
Examples
Embodiment 1
[0033] Add the high-efficiency composite additive in the present invention in the 1# absorption tower and account for 550ppm of the total amount of the slurry, according to the following components and mass percentages: 40% adipic acid, 20% sodium acetate, 20% potassium acetate, dodecane Sodium phenyl sulfonate 10%, manganese sulfate 3%, polysiloxane 2%, sodium chloride 5%. At a unit load of 300MW, the SO2 inlet concentration of the desulfurization tower is 4195.3mg / Nm 3 , running 5 circulating slurry pumps, the concentration at the outlet of the desulfurization tower can reach 22.1mg / Nm 3 , the desulfurization efficiency is increased by 1.5%, and the slurry limestone is saved by 13.8%. The comparison of the main indicators of the blank test with additives and without additives is shown in Table 1.
Embodiment 2
[0035] Add the high-efficiency composite additive in the present invention to 1# absorption tower and account for 520ppm of the total amount of slurry, according to the following components and mass percentages: acetic acid 20%, adipic acid 20%, sodium formate 10%, sodium citrate 30% , Sodium Lauryl Sulfate 10%, Manganese Chloride 3%, Polyoxyethylene Ether 2%, Sodium Chloride 5%. When the load of the unit is 300MW, the SO2 inlet concentration of the desulfurization tower is 4215.4mg / Nm3 , running 5 circulating slurry pumps, the concentration at the outlet of the desulfurization tower can reach 25.9mg / Nm 3 , the desulfurization efficiency is increased by 1.5%, and the slurry limestone is saved by 10.9%. The comparison of the main indicators of the blank test with additives and without additives is shown in Table 2.
Embodiment 3
[0037] Add the high-efficiency composite additive in the present invention in the 1# absorption tower and account for 500ppm of the total amount of the slurry, according to the following components and mass percentages: 20% formic acid, 20% adipic acid, 20% sodium formate, 20% sodium acetate, Sodium Lauryl Sulfate 6%, Lauryl Sultaine 4%, Manganese Chloride 3%, Polysiloxane 2%, Sodium Sulfate 5%. When the unit load is 300MW, the SO2 inlet concentration of the desulfurization tower is 4227.8mg / Nm 3 , running 5 circulating slurry pumps, the concentration at the outlet of the desulfurization tower can reach 22.7mg / Nm 3 , the desulfurization efficiency is increased by 1.5%, and the slurry limestone is saved by 15.6%. Add additive and do not add additive blank test main index contrast, as shown in table 3; Add the real-time concentration monitoring of absorption tower outlet flue gas after adding additive of the present invention, as shown in Table 3 figure 1 shown. figure 1 It r...
PUM
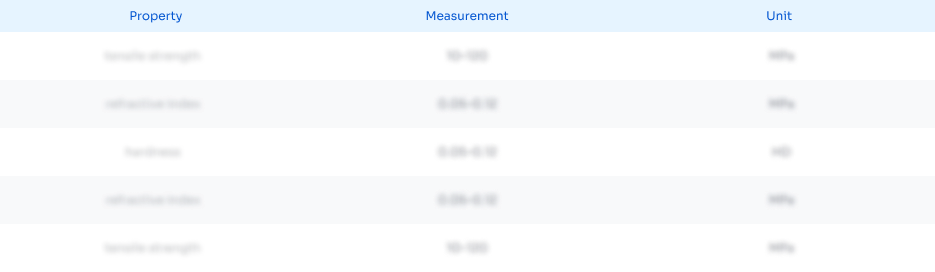
Abstract
Description
Claims
Application Information

- R&D Engineer
- R&D Manager
- IP Professional
- Industry Leading Data Capabilities
- Powerful AI technology
- Patent DNA Extraction
Browse by: Latest US Patents, China's latest patents, Technical Efficacy Thesaurus, Application Domain, Technology Topic, Popular Technical Reports.
© 2024 PatSnap. All rights reserved.Legal|Privacy policy|Modern Slavery Act Transparency Statement|Sitemap|About US| Contact US: help@patsnap.com