Method for treating molten salt electrolysis cathode deposits through pyrogenic process
A molten salt electrolysis and pyroprocessing technology, applied in the field of electrochemical metallurgy, can solve the problems of waste of resources and energy, unsuitable for continuous production, increase of procedures and production costs, etc., to reduce processing costs, improve theoretical significance and application Value, the effect of avoiding waste of resources and energy
- Summary
- Abstract
- Description
- Claims
- Application Information
AI Technical Summary
Problems solved by technology
Method used
Examples
Embodiment 1
[0024] Cathodic deposits (including metal hafnium and hafnium low-valent compounds and bonded molten salt electrolytes) obtained by electrolysis and electrorefining of hafnium by pyrolysis, using the following steps:
[0025] (1) The cathode deposit obtained by electrolysis and electrolytic refining of hafnium is broken into particles with a particle size of 2 to 5 mm and mixed with NaCl-KCl-NaF electrolyte in an equimolar ratio, and the content of the cathode deposit is 20% to 30% (mass ratio), and then loaded into a ceramic crucible with a porosity of 70-90%.
[0026] (2) Put the ceramic crucible into the vacuum melting filter tank. After the canning is completed, vacuumize and heat slowly at a heating rate of 5-8°C / min until the pressure reaches -3 Pa, stop vacuuming, and continue to heat up to 700-750°C to keep warm.
[0027] (3) After 30 to 50 minutes of heat preservation, fill the upper part of the equipment with argon to maintain a slight positive pressure of 200 to 40...
Embodiment 2
[0030] The cathodic deposit obtained by pyrolysis and electrolytic refining of zirconium (including metal zirconium and low-valent compounds of zirconium and bonded molten salt electrolyte) adopts the following steps:
[0031](1) The cathode deposit obtained by electrolysis and electrolytic refining of zirconium is broken into particles with a particle size of 2 to 5 mm and mixed with NaCl-KCl-NaF electrolyte in an equimolar ratio, and the content of the cathode deposit is 20% to 30% (mass ratio), and then loaded into a ceramic crucible with a porosity of 70-90%.
[0032] (2) Put the ceramic crucible into the vacuum melting filter tank. After the canning is completed, vacuumize and heat slowly at a heating rate of 5-8°C / min until the pressure reaches -3 Pa, stop vacuuming, and continue to heat up to 700-750°C to keep warm.
[0033] (3) After 30 to 50 minutes of heat preservation, fill the upper part of the equipment with argon to maintain a slight positive pressure of 200 to ...
Embodiment 3
[0036] The cathodic deposit obtained by pyrolysis and electrolytic refining of titanium (including metal titanium and titanium low-valent compounds and bonded molten salt electrolyte) adopts the following steps:
[0037] (1) The cathode deposit obtained by electrolysis and electrolytic refining titanium is broken into particles with a particle size of 2 to 5 mm and mixed with NaCl-KCl-NaF electrolyte in an equimolar ratio, and the content of the cathode deposit is 20% to 30% (mass ratio), and then loaded into a ceramic crucible with a porosity of 70-90%.
[0038] (2) Put the ceramic crucible into the vacuum melting filter tank. After the canning is completed, vacuumize and heat slowly at a heating rate of 5-8°C / min until the pressure reaches -3 Pa, stop vacuuming, and continue to heat up to 700-750°C to keep warm.
[0039] (3) After 30 to 50 minutes of heat preservation, fill the upper part of the equipment with argon to maintain a slight positive pressure of 200 to 400 Pa hi...
PUM
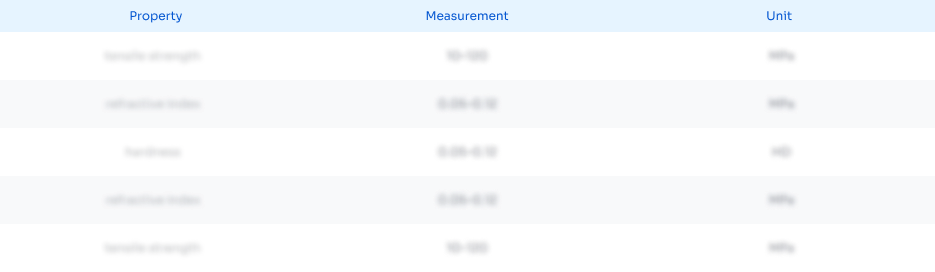
Abstract
Description
Claims
Application Information

- Generate Ideas
- Intellectual Property
- Life Sciences
- Materials
- Tech Scout
- Unparalleled Data Quality
- Higher Quality Content
- 60% Fewer Hallucinations
Browse by: Latest US Patents, China's latest patents, Technical Efficacy Thesaurus, Application Domain, Technology Topic, Popular Technical Reports.
© 2025 PatSnap. All rights reserved.Legal|Privacy policy|Modern Slavery Act Transparency Statement|Sitemap|About US| Contact US: help@patsnap.com