Process for preparing permanent magnetic ferrite through two-stage ball milling and mixture
A permanent ferrite and preparation technology, applied in the field of magnetic materials, can solve the problems of easy cracking of pores and products, strontium running, etc., and achieve the effect of not easy to precipitate, slow layering, and small molecular weight
- Summary
- Abstract
- Description
- Claims
- Application Information
AI Technical Summary
Problems solved by technology
Method used
Examples
Embodiment 1
[0017] ① Add ferrite pre-fired material, steel balls and water into the ball mill according to the mass ratio of 1:4:1.5, turn on the ball mill, set its speed to 29r / min, and mix for 15 minutes;
[0018] ②Add boric acid with 0.2% mass of pre-fired ferrite to the above mixture in summer, then add ammonium bicarbonate with 2.0% mass of pre-fired ferrite, set the speed at 29r / min, and mix for 30min;
[0019] ③Start ball milling, set the speed of the ball mill to 29r / min, continuously shower the outside with a large amount of water, measure the temperature of the internal mixture at 50-55°C, and the ball milling time is 15h;
[0020] ④ After the ball milling is finished, the material is discharged, and the ball mill is placed in the sedimentation tower for natural precipitation for 72 hours;
[0021] ⑤Remove the water in the upper layer of the mixed material after precipitation, and then take out the material while stirring under the stirring condition of 180r / min.
Embodiment 2
[0023] ① Add ferrite pre-fired material, steel balls and water into the ball mill according to the mass ratio of 2:4:2.5, turn on the ball mill, set its speed to 29r / min, and mix for 15 minutes;
[0024] ②Add boric acid with 0.1% mass of ferrite pre-sintered material to the above mixture in spring, then add ammonium bicarbonate with 0.7% mass of ferrite pre-sintered material, set the speed at 29r / min, and mix for 30 minutes;
[0025] ③Start ball milling, set the speed of the ball mill to 29r / min, continuously shower the outside with a large amount of water, measure the temperature of the internal mixture to be 45-50°C, and the ball milling time to be 16h;
[0026] ④ After the ball milling is finished, the material is discharged, and the ball mill is placed in the sedimentation tower for natural precipitation for 72 hours;
[0027] ⑤Remove the water in the upper layer of the mixed material after precipitation, and then take out the material while stirring under the stirring con...
Embodiment 3
[0029] ① Add ferrite pre-fired material, steel balls and water into the ball mill according to the mass ratio of 1:5:2.5, turn on the ball mill, set its speed to 29r / min, and mix for 15 minutes;
[0030] ②Add boric acid with 0.1% mass of ferrite pre-fired material to the above mixture in autumn, and then add ammonium bicarbonate with 0.8% mass of ferrite pre-fired material, set the speed at 29r / min, and mix for 30min;
[0031] ③Start ball milling, set the speed of the ball mill to 29r / min, continuously shower the outside with a large amount of water, measure the temperature of the internal mixture at 45-50°C, and the ball milling time is 14h;
[0032] ④ After the ball milling is finished, the material is discharged, and the ball mill is placed in the sedimentation tower for natural precipitation for 72 hours;
[0033] ⑤Remove the water in the upper layer of the mixed material after precipitation, and then take out the material while stirring under the stirring condition of 180...
PUM
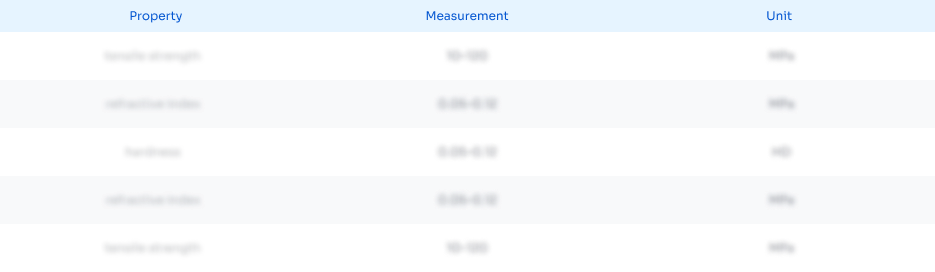
Abstract
Description
Claims
Application Information

- Generate Ideas
- Intellectual Property
- Life Sciences
- Materials
- Tech Scout
- Unparalleled Data Quality
- Higher Quality Content
- 60% Fewer Hallucinations
Browse by: Latest US Patents, China's latest patents, Technical Efficacy Thesaurus, Application Domain, Technology Topic, Popular Technical Reports.
© 2025 PatSnap. All rights reserved.Legal|Privacy policy|Modern Slavery Act Transparency Statement|Sitemap|About US| Contact US: help@patsnap.com