Reaction apparatus for producing styrene by dehydrogenation of low pressure drop ethylbenzene
A technology for ethylbenzene dehydrogenation production and reaction device, which is applied in the direction of feeding device, hydrocarbons, hydrocarbons, etc., can solve the problems of inability to meet the low pressure drop of azeotropic heat recovery and energy saving process, and achieves reduction of mixing pressure drop, Improve the effect of mixing uniformity
- Summary
- Abstract
- Description
- Claims
- Application Information
AI Technical Summary
Problems solved by technology
Method used
Image
Examples
Embodiment 1
[0059] The two-stage negative pressure intermediate reheating reaction system of ethylbenzene dehydrogenation to styrene using azeotropic heat recovery and energy-saving technology adopts such as image 3 The structure type of the reaction device for the production of styrene from ethylbenzene dehydrogenation with ultra-low pressure drop is shown, the diameter of the reactor is 4200 mm, the thickness of the catalyst bed is 600 mm, and the height is 18000 mm. The height-thickness ratio (value) of the catalyst bed is 30, and the catalyst seal height The angle α between the upper baffle and the horizontal plane of the biconical baffle is 74° and the angle β between the lower baffle and the horizontal plane of the biconical baffle is 60°. The diameter of the inner distribution cylinder is 1800mm, and the pitch t of the spiral baffle is 5000mm. The diversion nozzle of the mixer is 4, the diameter of the short pipe is 300mm, and the diameter of the mixing degree adjustment hole is 8...
Embodiment 2
[0061] The two-stage negative pressure intermediate reheating reaction system of ethylbenzene dehydrogenation to styrene using azeotropic heat recovery and energy-saving technology adopts such as image 3 The structure type of the reaction device for the production of styrene from ethylbenzene dehydrogenation with ultra-low pressure drop is shown, the diameter of the reactor is 3100mm, the thickness of the catalyst bed is 550mm, and the height is 11000mm. The height-thickness ratio (value) of the catalyst bed is 20, and the catalyst seal height The angle α between the upper baffle and the horizontal plane of the biconical baffle is 79° and the angle β between the lower baffle and the horizontal plane of the biconical baffle is 45°. The diameter of the inner distribution cylinder is 1400mm, and the pitch t of the spiral baffle is 2000mm. The diversion nozzle of the mixer is 6, the diameter of the short tube is 175mm, and the diameter of the mixing degree adjustment hole is 50mm...
PUM
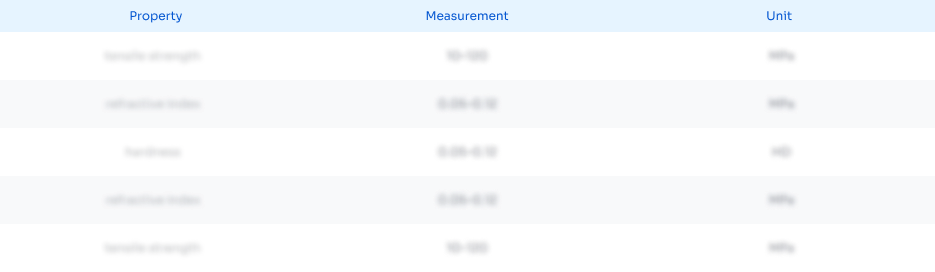
Abstract
Description
Claims
Application Information

- R&D
- Intellectual Property
- Life Sciences
- Materials
- Tech Scout
- Unparalleled Data Quality
- Higher Quality Content
- 60% Fewer Hallucinations
Browse by: Latest US Patents, China's latest patents, Technical Efficacy Thesaurus, Application Domain, Technology Topic, Popular Technical Reports.
© 2025 PatSnap. All rights reserved.Legal|Privacy policy|Modern Slavery Act Transparency Statement|Sitemap|About US| Contact US: help@patsnap.com