A Thickness Optimization Design Method of Turbine Blade Thermal Barrier Coating
A technology for turbine blade and thickness optimization, applied in the field of surface coating protection, can solve the problems of inability to optimize the thickness distribution design, lack of evaluation of the pros and cons of TBCs thickness design, achieve simple and efficient TBCs thickness optimization design, reduce the amount of analysis and calculation, Effects of low stress levels
- Summary
- Abstract
- Description
- Claims
- Application Information
AI Technical Summary
Problems solved by technology
Method used
Image
Examples
Embodiment Construction
[0048] The present invention will be further described in detail below in conjunction with specific embodiments, which are to explain rather than limit the present invention.
[0049] The optimized design process of the present invention is as follows figure 1 As shown, in order to better understand the technical solution of the present invention, the above optimization design method is applied to the TBCs thickness design of gas turbine turbine blades. figure 2 shown.
[0050] The specific process of this embodiment includes the following steps:
[0051] Step 1: Determine the thickness of each layer of TBCs.
[0052] The TBCs comprise a ceramic layer, an adhesive layer and a thermally grown oxide layer. The thickness of the selected ceramic layer is k×100 μm, where k is the number of the analysis times, that is, the repetition times of step 1 to step 6, k=1, 2, . . . , 10. The thickness of the adhesive layer selected in this embodiment is 150 μm, and the thickness of the...
PUM
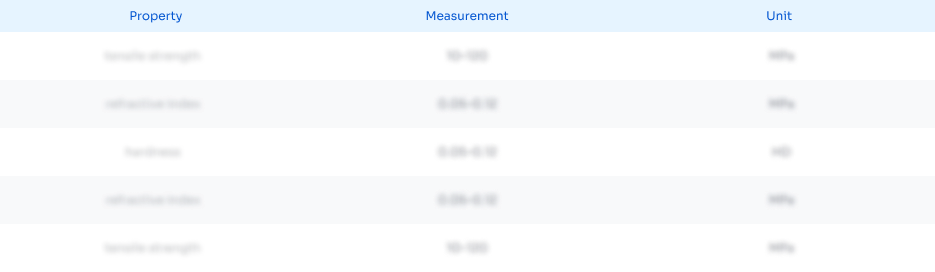
Abstract
Description
Claims
Application Information

- Generate Ideas
- Intellectual Property
- Life Sciences
- Materials
- Tech Scout
- Unparalleled Data Quality
- Higher Quality Content
- 60% Fewer Hallucinations
Browse by: Latest US Patents, China's latest patents, Technical Efficacy Thesaurus, Application Domain, Technology Topic, Popular Technical Reports.
© 2025 PatSnap. All rights reserved.Legal|Privacy policy|Modern Slavery Act Transparency Statement|Sitemap|About US| Contact US: help@patsnap.com