Belt pulley
A pulley and ring technology, applied in belts/chains/gears, components with teeth, portable lifting devices, etc., can solve the problems of long production cycle, poor dimensional accuracy of pulley parts, and poor product quality, and save production. cost, improved labor conditions, and the effect of reducing equipment investment
- Summary
- Abstract
- Description
- Claims
- Application Information
AI Technical Summary
Problems solved by technology
Method used
Image
Examples
Embodiment 1
[0028] The process steps of direct casting groove shape of rear axle clutch pulley of three-wheeled automobile are as follows:
[0029] (1) According to the groove shape requirements of the rear axle clutch pulley of the three-wheeled automobile, at first make a shell shape completely consistent with its groove shape as a master mold;
[0030] (2) Make the outer shape of the shell mold. The outer shape of the shell mold is required to be matched with the core shooter of coated sand. The outer dimension of the shell mold is required to be the maximum size of the master mold plus 8mm. When mating, its wall thickness is guaranteed to be 8mm;
[0031] (3) Fix the master mold on the workbench of the sand shooting machine, and close the iron mold shape, heat it to 260°C and keep it warm for 30 minutes to shoot the sand;
[0032] (4) Shoot the coated sand onto the pre-designed iron mold through the sand shooting hole of the sand shooting machine, so that the coated sand fills the ca...
Embodiment 2
[0037] The process steps of direct casting groove shape of rear axle clutch pulley of three-wheeled agricultural vehicles are as follows:
[0038] (1) According to the groove shape requirements of the three-wheel agricultural steam rear axle clutch pulley, firstly make a model that is completely consistent with its groove shape as the master mold;
[0039] (2) Make the outer shape of the shell mold. The shape of the shell mold is required to be matched with the core shooter of the coated sand. The inner size of the cavity is required to be the maximum size of the master mold plus 8mm, so that the inner cavity of the outer shape of the shell mold is matched with the groove-shaped master mold model. When the wall thickness is guaranteed to be 8mm;
[0040] (3) Fix the master mold on the workbench of the sand shooting machine, and close the shape of the hot core box, heat it to 260°C and keep it warm for 30 minutes to shoot the sand;
[0041] (4) Shoot the coated sand into the p...
Embodiment 3
[0046] The process steps of direct casting groove shape of rear axle clutch pulley of three-wheeled agricultural vehicles are as follows:
[0047] (1) According to the groove shape requirements of the rear axle clutch pulley of the three-wheeled agricultural vehicle, first make a model that is completely consistent with its groove shape as a master mold;
[0048] (2) Make the outer shape of the shell mold. The shape of the shell mold is required to be matched with the core shooter of the coated sand. The inner size of the cavity is required to be the maximum size of the master mold plus 8mm, so that the inner cavity of the outer shape of the shell mold is matched with the groove-shaped master mold model. When the wall thickness is guaranteed to be 8mm;
[0049] (3) Fix the master mold on the workbench of the sand shooting machine, and close the shape of the hot core box, heat it to 280°C and keep it warm for 30 minutes to shoot the sand;
[0050] (4) Shoot the coated sand int...
PUM
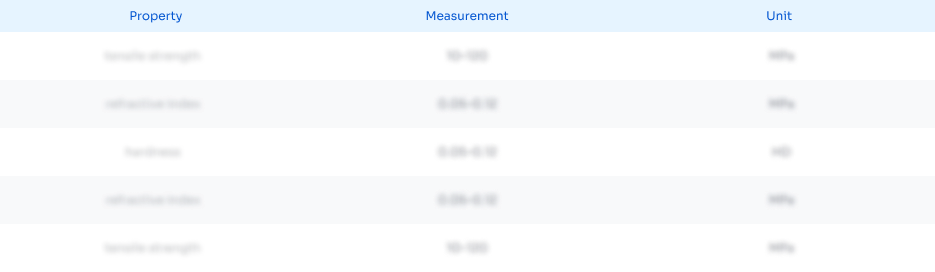
Abstract
Description
Claims
Application Information

- R&D
- Intellectual Property
- Life Sciences
- Materials
- Tech Scout
- Unparalleled Data Quality
- Higher Quality Content
- 60% Fewer Hallucinations
Browse by: Latest US Patents, China's latest patents, Technical Efficacy Thesaurus, Application Domain, Technology Topic, Popular Technical Reports.
© 2025 PatSnap. All rights reserved.Legal|Privacy policy|Modern Slavery Act Transparency Statement|Sitemap|About US| Contact US: help@patsnap.com