Preparation method of ZSM-48 molecular sieve
A molecular sieve and organic base technology, applied in the direction of crystalline aluminosilicate zeolite, etc., can solve the problem that the pure phase ZSM-48 molecular sieve cannot be synthesized, and achieve the effect of good catalytic performance and high crystallinity
- Summary
- Abstract
- Description
- Claims
- Application Information
AI Technical Summary
Problems solved by technology
Method used
Image
Examples
example 1
[0034] Add 7.5 g (0.047 mol) of bis(dimethylaminoethyl) ether and 100 mL of isopropanol into a two-necked flask, and stir evenly. At 25°C, 11.4g (0.047mol) of 1,6-dibromohexane was slowly added dropwise, heated to reflux temperature for 30min, the solution changed from colorless to white turbidity, and then reacted at reflux temperature for 12h, cooled to 25 ℃, 150 mL of ethyl acetate was added and stirred for 15 min. Filtration, the obtained solid was washed with ethyl acetate to give 13.1 g of white solid as 4,4,11,11-tetramethyl-1-oxo-4,11-diazacyclotridecane-4,11-di Bromide salt, i.e. the compound in which n is 4 in formula (I), its melting point is 230°C, 1 H-NMR spectrum chemical shift (300MHz, internal standard TMS, solvent D 2 O) is: 1.36(4H,t), 1.17(4H,t), 3.06(12H,s), 3.33(4H,t), 3.56(4H,t), 3.93(4H,t).
example 2
[0036] The diazoxane dibromide salt was prepared as in Example 1, except that 12.06 g (0.047 mol) of 1,8-dibromooctane was used instead of 1,6-dibromohexane to give 4,4, 13,13-tetramethyl-1-oxo-4,13-diazacyclopentadecane-4,13-dibromo salt 14.08g, i.e. the compound of formula (I) where n is 6, its melting point is 230.3°C, 1 H-NMR spectrum chemical shift (300MHz, internal standard TMS, solvent CDCl 3 )δ(ppm): 1.36(t, 4H), 1.73(s, 4H), 3.05(s, 12H), 3.33(t, 4H), 3.56(t, 4H), 3.92(t, 4H).
example 3
[0038] Take 0.134g of sodium metaaluminate and add it to a 45mL polytetrafluoroethylene (Teflon) container, add 14.45g of deionized water, 13.69g of tetraethylammonium hydroxide solution with a concentration of 35% by mass, 1.976g of 4,4, 11,11-Tetramethyl-1-oxo-4,11-diazacyclotridecane-4,11-dibromo salt was used as structure directing agent (R), stirred for 30 minutes until uniform, and then added 2g white carbon black , stir for 5 minutes and mix thoroughly, wherein the molar ratio of each component is: SiO 2 / Al 2 O 3 =40, TEAOH / SiO 2 =1.0, H 2 O / SiO 2 =40, R / SiO 2 =0.15, Na 2 O / SiO 2 = 0.12.
[0039] The above mixture was put into a 45 mL steel autoclave with Teflon lining, capped and sealed, and the autoclave was placed in a rotating convection oven with a rotating speed of 20 rpm, reacted at 120° C. for 4 days, and then heated to 160 °C. °C for 10 days. Take out the autoclave and make it rapidly cooled to room temperature, separate the mixture on a high-speed c...
PUM
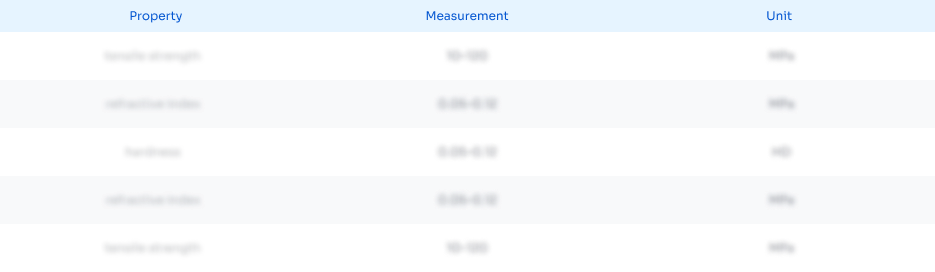
Abstract
Description
Claims
Application Information

- R&D
- Intellectual Property
- Life Sciences
- Materials
- Tech Scout
- Unparalleled Data Quality
- Higher Quality Content
- 60% Fewer Hallucinations
Browse by: Latest US Patents, China's latest patents, Technical Efficacy Thesaurus, Application Domain, Technology Topic, Popular Technical Reports.
© 2025 PatSnap. All rights reserved.Legal|Privacy policy|Modern Slavery Act Transparency Statement|Sitemap|About US| Contact US: help@patsnap.com