Height and speed testing structure and method based on minimum gas path delay
A technology for testing structure and height, applied in the field of flight test, which can solve the problems of limited space for the front pitot tube and setting test sensors for the front pitot tube
- Summary
- Abstract
- Description
- Claims
- Application Information
AI Technical Summary
Problems solved by technology
Method used
Image
Examples
Embodiment Construction
[0010] The altitude velocity test structure based on the minimum gas path delay includes a front branch pitot tube 1, a height velocity sensor 3 is arranged in the front branch pitot tube 1, and the altitude velocity sensor 3 is fixed on the static pressure port according to its size. 2 The nearest position, and sealed connection with the total pressure air circuit and static pressure air circuit, using digital transmission. The altitude velocity test method based on the minimum air path delay adopts the above altitude velocity test structure, and the altitude velocity test is performed at the position closest to the static pressure port 2 .
PUM
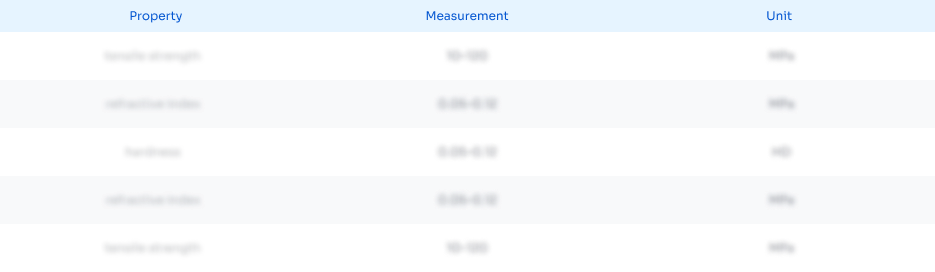
Abstract
Description
Claims
Application Information

- R&D Engineer
- R&D Manager
- IP Professional
- Industry Leading Data Capabilities
- Powerful AI technology
- Patent DNA Extraction
Browse by: Latest US Patents, China's latest patents, Technical Efficacy Thesaurus, Application Domain, Technology Topic, Popular Technical Reports.
© 2024 PatSnap. All rights reserved.Legal|Privacy policy|Modern Slavery Act Transparency Statement|Sitemap|About US| Contact US: help@patsnap.com