Catalyst for butene oxidative dehydrogenation preparation of butadiene and preparation method thereof
A technology for oxidative dehydrogenation and catalysts, applied in metal/metal oxide/metal hydroxide catalysts, carbon compound catalysts, physical/chemical process catalysts, etc., can solve the problem of low selectivity of butadiene and deep oxidation products CO2 and other problems, to achieve good performance, reduce the production of CO2, high conversion rate of butene
- Summary
- Abstract
- Description
- Claims
- Application Information
AI Technical Summary
Problems solved by technology
Method used
Image
Examples
Embodiment 1
[0024] Weigh an appropriate amount of high-purity ferric nitrate and magnesium nitrate and mix them in 1L of deionized water, and stir evenly. Then the above solution is co-precipitated with 20% ammonia solution, the precipitation pH value is kept at 9.5, and the precipitation temperature is room temperature, then the solid sample in the precipitated product is separated with a centrifuge, washed with 4L deionized water, and the obtained solid Dry in an oven at 110°C for 4 hours. The dried sample was calcined in a muffle furnace at 600°C for 4 hours to obtain catalyst A, which was ground into 40-60 mesh particles for catalyst evaluation. The Fe-containing component of catalyst A consists of Fe 2 o 3 2MgFe 2 o 4 , the catalyst also contains Li 70ppm, Ca 200ppm, and Ti 150ppm in mass fraction.
Embodiment 2
[0026] Weigh an appropriate amount of high-purity ferric nitrate and magnesium nitrate and mix them in 1L of deionized water, and stir evenly. Then the above solution is co-precipitated with 10% ammonia solution, the precipitation pH value is maintained at 6.0, and the precipitation temperature is 10°C, then the solid sample in the precipitated product is separated with a centrifuge, washed with 4L deionized water, and the resulting The solid was dried in an oven at 90°C for 24 hours. The dried sample was calcined in a muffle furnace at 400°C for 24 hours to obtain catalyst B, which was ground into 40-60 mesh particles for catalyst evaluation. The Fe-containing component of catalyst B consists of Fe 2 o 3 20MgFe 2 o 4 , the catalyst also contains Li 95ppm, Ca 260ppm, and Ti 180ppm in mass fraction.
Embodiment 3
[0028] Weigh an appropriate amount of high-purity ferric nitrate and magnesium nitrate into 1L of deionized water, and stir evenly. Then the above solution is co-precipitated with 30% ammonia solution, the precipitation pH value is maintained at 12, and the precipitation temperature is 80 ° C. Then, the solid sample in the precipitated product is separated with a centrifuge, washed with 4L deionized water, and the resulting The solid was dried in an oven at 150°C for 1 hour. The dried sample was calcined in a muffle furnace at 650°C for 1 hour to obtain catalyst C, which was ground into 40-60 mesh particles for catalyst evaluation. The composition of the Fe-containing component of catalyst C is 20Fe 2 o 3 1MgFe 2 o 4 , the catalyst also contains Li 50ppm, Ca 190ppm, and Ti 140ppm in mass fraction.
PUM
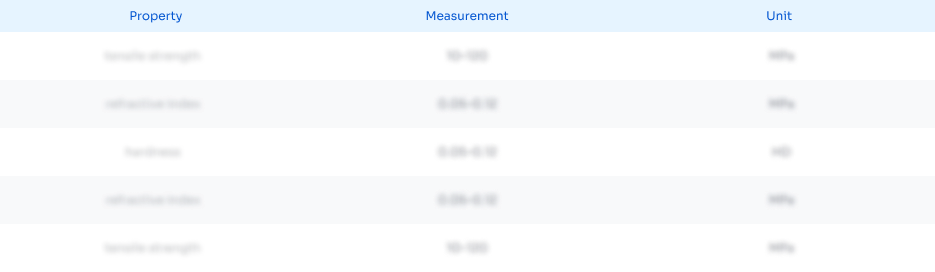
Abstract
Description
Claims
Application Information

- R&D
- Intellectual Property
- Life Sciences
- Materials
- Tech Scout
- Unparalleled Data Quality
- Higher Quality Content
- 60% Fewer Hallucinations
Browse by: Latest US Patents, China's latest patents, Technical Efficacy Thesaurus, Application Domain, Technology Topic, Popular Technical Reports.
© 2025 PatSnap. All rights reserved.Legal|Privacy policy|Modern Slavery Act Transparency Statement|Sitemap|About US| Contact US: help@patsnap.com