Double-robot base coordinate system calibration method based on laser tracker
A laser tracker and dual-robot technology, applied to instruments, optical devices, measuring devices, etc., can solve the problems of the calibration results being affected by human errors, the tedious and time-consuming teaching process, and the tedious preparation work, etc., so as to avoid the calibration accuracy. Influence, improve the calibration efficiency, shorten the time effect
- Summary
- Abstract
- Description
- Claims
- Application Information
AI Technical Summary
Problems solved by technology
Method used
Image
Examples
Embodiment 1
[0040] Such as figure 1 As shown, the laser tracker is set up near the dual robots, and the magnetic target ball seat is adsorbed on the end flange of the robot. The target ball of the laser tracker is placed on the target ball seat to ensure that the position of the target ball is fixed during the calibration process. Do not move.
[0041] Control the robot so that it is in the zero position. Control the first axis of the robot to perform single-axis rotation, and the other five axes do not rotate. Record the coordinates of the center of the target ball at certain angles, record n points in total, and obtain the point group P1=(x P1i ,y P1i ,z P1i )(i=1,2...n), return the robot to the zero point after the rotation is completed.
[0042] Control the second axis of the robot to perform single-axis rotation, and the other five axes do not rotate. Record the coordinates of the center of the target ball at certain angles, record n points in total, and obtain the point grou...
Embodiment 2
[0051] The laser tracker and supporting data processing software Spatial Analyzer are used to realize rapid calibration and greatly improve the calibration efficiency.
[0052] Such as figure 1 As shown, the laser tracker is set up near the dual robots, and the magnetic target ball seat is adsorbed on the end flange of the robot. The target ball of the laser tracker is placed on the target ball seat to ensure that the position of the target ball is fixed during the calibration process. Do not move.
[0053] Control the robot so that it is in the zero position. Control the first axis of the robot to perform single-axis rotation, and the other five axes do not rotate. Record the coordinates of the center of the target ball in the Spatial Analyzer at certain angles, record n points in total, and obtain the point group P1=(x P1i ,y P1i ,z P1i )(i=1,2...n), return the robot to the zero point after the rotation is completed.
[0054] Control the second axis of the robot to pe...
PUM
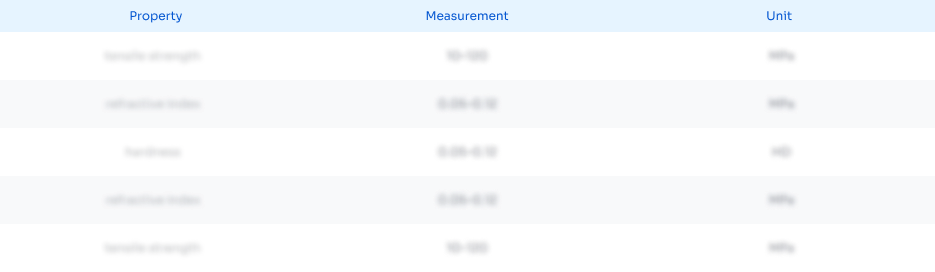
Abstract
Description
Claims
Application Information

- R&D Engineer
- R&D Manager
- IP Professional
- Industry Leading Data Capabilities
- Powerful AI technology
- Patent DNA Extraction
Browse by: Latest US Patents, China's latest patents, Technical Efficacy Thesaurus, Application Domain, Technology Topic, Popular Technical Reports.
© 2024 PatSnap. All rights reserved.Legal|Privacy policy|Modern Slavery Act Transparency Statement|Sitemap|About US| Contact US: help@patsnap.com