Steel surface blueing solution and blueing treatment technology thereof
A processing technology and steel technology, applied in the direction of metal material coating process, etc., can solve the problem of uneven film formation of bluing film, and achieve the effect of reducing the cost of bluing, uniform film formation and good surface quality
- Summary
- Abstract
- Description
- Claims
- Application Information
AI Technical Summary
Problems solved by technology
Method used
Examples
Embodiment 1
[0039] A steel surface bluing solution provided in this example has the following chemical components in mass percent: sodium phosphate: 6%; sodium nitrate: 3%; sodium hydroxide: 10%; sodium nitrite: 8%; triethanolamine: Potassium nitrate: 6%; Passivator 2%; Phosphating accelerator: 1%; Surplus is water; The chemical composition mass percentage of described phosphating accelerator is: sodium nitrite: 13%, magnesium oxide : 8%, phosphoric acid: 3%, sodium dodecylbenzene sulfonate: 1%, salicylic acid: 1%; EDTA: 2%, balance is zinc oxide; The chemical composition mass percent of described passivating agent is : Nitric acid: 6%, phosphoric acid: 12-15%, hydrogen peroxide 5%, urotropine: 0.5%, zinc phosphate 1%, magnesium nitrate 5%, sodium alkyl sulfate: 1%, the balance is water .
[0040] This embodiment utilizes the process of steel surface bluing processing steel, including the following steps: sample → cold water cleaning → chemical degreasing → hot water washing → cold water...
Embodiment 2
[0047] A steel surface bluing solution provided in this example has the following mass percentages of chemical components: sodium phosphate: 8%; sodium nitrate: 4%; sodium hydroxide: 12%; sodium nitrite: 9%; triethanolamine: 1%; Potassium nitrate: 8%; Passivator: 3%; Phosphating accelerator: 1%; Magnesium: 10%, phosphoric acid: 4%, sodium dodecylbenzenesulfonate: 2%, salicylic acid: 2%; EDTA: 3%, the balance is zinc oxide; the chemical composition mass percentage of the passivating agent For: Nitric acid: 7%, Phosphoric acid: 13%, Hydrogen peroxide: 7%, Methanol: 1%, Zinc phosphate: 2%, Magnesium nitrate: 7%, Sodium alkyl sulfate: 2%, The balance is water.
[0048] This embodiment utilizes the process of steel surface bluing processing steel, including the following steps: sample → cold water cleaning → chemical degreasing → hot water washing → cold water cleaning → pickling and derusting → water washing → bluing → water washing and drying quickly → finished product ;
[004...
Embodiment 3
[0054] A steel surface bluing solution provided in this example has the following mass percentages of chemical components: sodium phosphate: 10%; sodium nitrate: 5%; sodium hydroxide: 15%; sodium nitrite: 10%; triethanolamine: 2%; potassium nitrate: 12%; passivator: 4%; phosphating accelerator: 2%; the balance is water;
[0055] The mass percent of the chemical composition of the phosphating accelerator is: sodium nitrite: 18%, magnesium oxide: 11%, phosphoric acid: 6%, sodium dodecylbenzenesulfonate: 3%, salicylic acid: 2%; EDTA: 4%, the balance is zinc oxide;
[0056] The mass percent of the chemical composition of the passivating agent is: nitric acid: 8%, phosphoric acid: 15%, hydrogen peroxide: 8%, methenamine: 1%, zinc phosphate: 5%, magnesium nitrate: 10%, alkane Sodium base sulfate: 3%, the balance is water.
[0057] This embodiment utilizes the process of steel surface bluing processing steel, including the following steps: sample → cold water cleaning → chemical de...
PUM
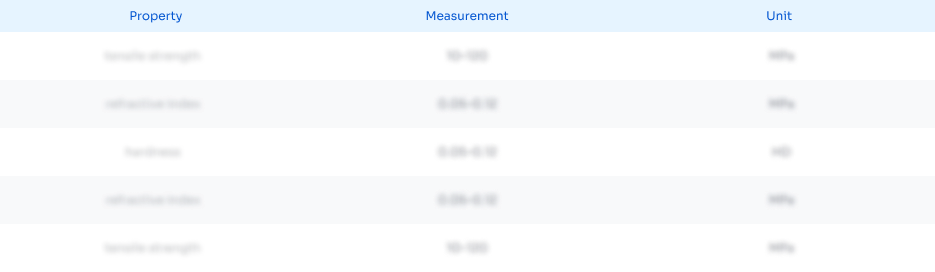
Abstract
Description
Claims
Application Information

- Generate Ideas
- Intellectual Property
- Life Sciences
- Materials
- Tech Scout
- Unparalleled Data Quality
- Higher Quality Content
- 60% Fewer Hallucinations
Browse by: Latest US Patents, China's latest patents, Technical Efficacy Thesaurus, Application Domain, Technology Topic, Popular Technical Reports.
© 2025 PatSnap. All rights reserved.Legal|Privacy policy|Modern Slavery Act Transparency Statement|Sitemap|About US| Contact US: help@patsnap.com