3D printing method and printing device for extrusion molding
A 3D printing and extrusion molding technology, applied in the field of 3D printing, can solve the problems of inability to print macro-aperture, limit the degree of freedom of printing functions, and have a large impact on the gravity of the printing line, so as to improve the narrowing of the printing line path and the improvement of the meniscus. Problems, the overall function is convenient and reliable, and the effect of increasing the size of the macro aperture
- Summary
- Abstract
- Description
- Claims
- Application Information
AI Technical Summary
Problems solved by technology
Method used
Image
Examples
Embodiment 1
[0061] Based on low temperature deposition 3D printing (FT-FDM), the actual printing process of the nozzle is as follows:
[0062] Such as figure 2 As shown, the printing device includes a coaxial nozzle 201, a nozzle temperature control device 202, and a printing platform 203 in a cold environment. Among them, the material A loaded in the inner channel of the coaxial nozzle can be a solution of polymer printing materials such as PLGA and PCL in organic solvents such as 1,4-dioxane and acetone; An organic solvent that is the same but does not contain polymeric materials.
[0063] The composite material extruded through the coaxial nozzle 201 is provided with thermal insulation and heating by the nozzle temperature control device 202 before extrusion to avoid premature solidification. When the material is extruded on the printing platform 203 , since the printing platform 203 is placed in a cold environment, the composite material can be rapidly solidified by the low tempera...
Embodiment 2
[0066] The invention is applied to a cell 3D printer in the field of biological 3D printing. The printer can realize the printing of hydrogel with cells, and usually adopts a physical-chemical two-step cross-linking method to achieve curing, that is, the initial shape of the printed product is achieved through temperature control during printing, and a chemical cross-linking agent is added dropwise after printing to improve the product quality. mechanical strength. In a preferred embodiment, gelatin is used for preliminary setting, and sodium alginate-calcium chloride system is used for chemical crosslinking.
[0067] Applying the present invention, the coaxial nozzle is used for printing, the gelatin-sodium alginate composite gel is printed in the inner flow channel, and the gelatin is printed in the outer flow channel. Afterwards, chemical crosslinking is carried out to improve the mechanical strength of the composite gel, and the outer layer of gelatin is peeled off by tem...
Embodiment 3
[0069] The invention is applied to common fused deposition printing such as plastic printing, raw materials for inner channel printing, wax for outer channel printing and other sacrificial materials with lower melting point and better fluidity after melting. It can play a certain supporting role in the printing line shape, and can be easily removed by micro-heating after printing.
PUM
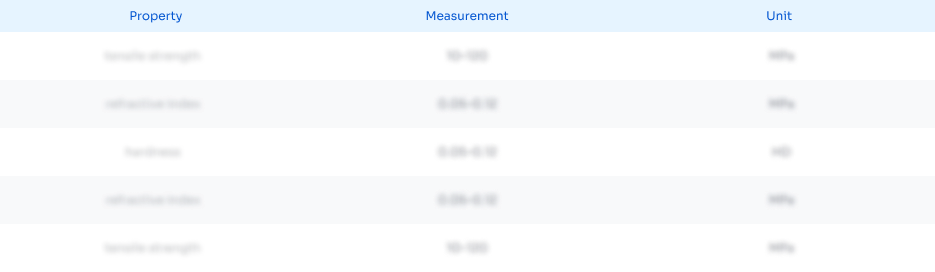
Abstract
Description
Claims
Application Information

- Generate Ideas
- Intellectual Property
- Life Sciences
- Materials
- Tech Scout
- Unparalleled Data Quality
- Higher Quality Content
- 60% Fewer Hallucinations
Browse by: Latest US Patents, China's latest patents, Technical Efficacy Thesaurus, Application Domain, Technology Topic, Popular Technical Reports.
© 2025 PatSnap. All rights reserved.Legal|Privacy policy|Modern Slavery Act Transparency Statement|Sitemap|About US| Contact US: help@patsnap.com