Production process for plate heat exchanger
A technology of plate heat exchanger and production process, which is applied in the field of heat exchanger processing, can solve the problems of non-pressure resistance, corrosion resistance, short service life, etc., and achieve the effect of ensuring service strength and service life, excellent quality, and simple and effective production process
- Summary
- Abstract
- Description
- Claims
- Application Information
AI Technical Summary
Problems solved by technology
Method used
Examples
Embodiment Construction
[0020] A production process for a plate heat exchanger, characterized in that it comprises the steps of:
[0021] a. Substrate treatment: The choice of the plate is 0.2-1.2mm stainless steel, nickel-based alloy or industrial pure titanium as the material of the plate, and the brazing solder layer is compounded on one or both sides of the plate; when the brazing solder When the layer is an elemental metal layer, the elemental metal is electroplated on the plate by electroplating; when the brazing solder layer is an alloy layer, the alloy layer is attached to the plate;
[0022] b. Substrate cutting: cutting the plates combined with the upper brazing solder layer into heat exchange plate substrate plates of corresponding specifications;
[0023] c. Stamping forming: the base material plate of the heat exchange plate that has been combined with the brazing solder layer and cut in step b is used to connect the knife, position and align the technology, and then use the whole plate ...
PUM
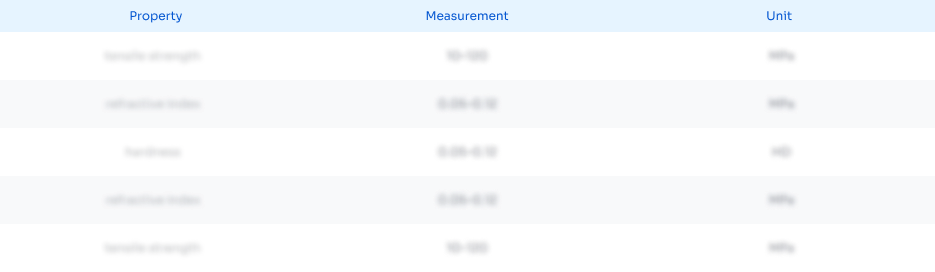
Abstract
Description
Claims
Application Information

- Generate Ideas
- Intellectual Property
- Life Sciences
- Materials
- Tech Scout
- Unparalleled Data Quality
- Higher Quality Content
- 60% Fewer Hallucinations
Browse by: Latest US Patents, China's latest patents, Technical Efficacy Thesaurus, Application Domain, Technology Topic, Popular Technical Reports.
© 2025 PatSnap. All rights reserved.Legal|Privacy policy|Modern Slavery Act Transparency Statement|Sitemap|About US| Contact US: help@patsnap.com