Long-carbon chain polyamide fiber and preparation method thereof
A carbon chain polyamide and fiber technology, applied in the field of modified polyamide fiber and its preparation, can solve problems such as poor hand feel, pollution, unusability, etc., and achieve broad industrial application prospects, ease dependence, and excellent tensile strength. Effect
- Summary
- Abstract
- Description
- Claims
- Application Information
AI Technical Summary
Problems solved by technology
Method used
Image
Examples
preparation example Construction
[0073]
[0074] The preparation method of long carbon chain polyamide fiber comprises the following steps:
[0075] (1) At least pentamethylenediamine and dibasic acid are used as raw materials to produce long carbon chain polyamide resins by melting method or solution thermal polycondensation method;
[0076] (2) Slices of polyamide resin with long carbon chains (slices are melted by a single-screw extruder) or melts are ejected from the spinneret to form a thin stream of melts through a screw, a metering pump and a spinning box;
[0077] (3) The fine flow of the melt is solidified into filaments through blowing;
[0078] (4) oiling, drafting and post-processing of the filament bundles to obtain long carbon chain polyamide fibers.
[0079] Wherein, in step (2), the temperature of the spinning box used to produce spinning is 210-290°C, preferably 230-280°C. The shape of the hole of the spinneret on the spinneret can be selected according to the cross-sectional shape of the...
Embodiment 1
[0105] The preparation method of polyamide 510 fiber in the present embodiment is as follows:
[0106] (1) Replace the air in a 100-liter polymerization kettle (K / SY166-2007 type) with nitrogen, add 30kg of pure water to the reaction kettle, and then add 10.06kg (98.5mol) of pentamethylenediamine (including renewable source of organic carbon), after stirring, add 19.93kg (98.5mol) sebacic acid, adjust the pH value to 7.7 with a small amount of pentamethylenediamine and sebacic acid (salt solution is diluted to 10% detection result), then add 0.9g Antioxidant H10, prepared nylon salt solution.
[0107] (2) Under a nitrogen environment, the temperature of the oil bath gradually rises to 280°C. When the pressure in the polymerization kettle rises to 1.73Mpa, start to exhaust. When the temperature in the kettle reaches 265°C, vacuumize to -0.06Mpa and maintain the vacuum degree After 20 minutes, polyamide 510 was prepared.
[0108] (3) Charge nitrogen into the polymerization ket...
Embodiment 2
[0118] The preparation method of polyamide 510 fiber in the present embodiment is as follows:
[0119](1) Replace the air in a 100-liter polymerization kettle (K / SY166-2007 type) with nitrogen, add 20kg of pure water to the reaction kettle, and then add 10.06kg (98.5mol) of pentamethylenediamine (including renewable source of organic carbon), after stirring, add 19.93kg (98.5mol) sebacic acid, adjust the pH value to 8.2 with a small amount of pentamethylenediamine and sebacic acid (dilute the salt solution to 10% detection result), then add 9g anti Oxygen H10, prepared polyamide salt solution.
[0120] (2) Under a nitrogen environment, the temperature of the oil bath is gradually raised to 280°C. After the pressure in the polymerization kettle rises to 1.73Mpa, the exhaust gas is started. When the temperature in the kettle reaches 245°C, add 90g of TiO 2 When the temperature in the kettle reaches 270°C, vacuumize to -0.08Mpa and keep the vacuum for 20min to prepare nylon 510....
PUM
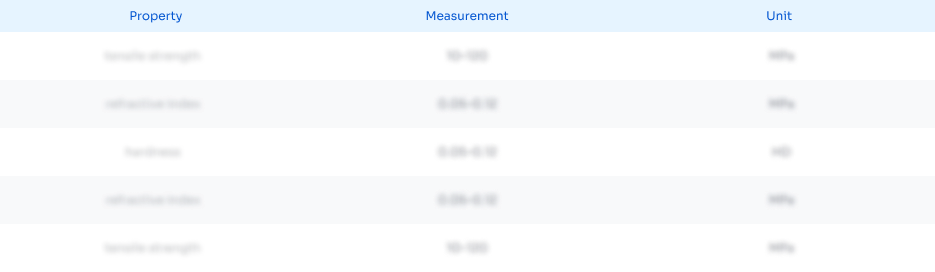
Abstract
Description
Claims
Application Information

- R&D
- Intellectual Property
- Life Sciences
- Materials
- Tech Scout
- Unparalleled Data Quality
- Higher Quality Content
- 60% Fewer Hallucinations
Browse by: Latest US Patents, China's latest patents, Technical Efficacy Thesaurus, Application Domain, Technology Topic, Popular Technical Reports.
© 2025 PatSnap. All rights reserved.Legal|Privacy policy|Modern Slavery Act Transparency Statement|Sitemap|About US| Contact US: help@patsnap.com