Method for preparing high temperature-resistant bismuth vanadate pigment
A bismuth vanadate, high temperature resistant technology, applied in inorganic pigment processing, chemical instruments and methods, fibrous fillers, etc., can solve problems such as poor compatibility
- Summary
- Abstract
- Description
- Claims
- Application Information
AI Technical Summary
Problems solved by technology
Method used
Examples
preparation example Construction
[0022] The present invention adopts following technical scheme: a kind of preparation method of high temperature resistant bismuth vanadate pigment comprises the following steps:
[0023] Step S1: Take the bismuth vanadate raw material, add water and stir quickly to form a dispersion, add acid to adjust the pH of the dispersion to 2.0-3.3;
[0024] Step S2: After the dispersion liquid is completely dispersed into a slurry, start to heat up, and raise the temperature to 50-100°C at a certain heating rate, and then operate at a constant temperature, drop the SiO-containing solution into the slurry 3 2- and OH - solution, the liquid addition time is 20-50 minutes, until the pH value rises to 12.0-12.5;
[0025] Step S3: Add acid to adjust the pH value of the solution to 6-7, precipitate the precipitate, filter the precipitate and wash it, add the precipitate to the solution containing PO 4 3- The solution is mixed uniformly and then dried to obtain a high temperature resistan...
Embodiment 1
[0036] Take 50g of commercially available coating-grade bismuth vanadate raw material, add 300g of water, stir and disperse rapidly for 30 minutes, add 3g of 80% glacial acetic acid, add nitric acid to adjust the pH value to 2.5, and start heating after the slurry is completely dispersed, at 3°C / Raise the temperature to 85°C at a rate of 1 minute, then operate at a constant temperature, drop in a solution formed by dissolving 30g sodium silicate nonahydrate and 10g NaOH in 200ml water, add liquid for 30 minutes, and the pH value rises to 12.2. After 10 minutes, use a mass Adjust the pH value to 6.5 with dilute nitric acid with a fraction of 10%. After 10 minutes, filter and wash, add 20g of trisodium phosphate dodecahydrate and 5g of water to the filter cake, mix well, and then dry at 90°C. After drying, the dry filter cake is crushed and ground into powder, and recorded as sample 1.
Embodiment 2
[0038] Take 50g of commercially available paint-grade bismuth vanadate raw material, add 400g of water, stir and disperse rapidly for 30 minutes, add 3g of 80% glacial acetic acid, add nitric acid to adjust the pH value to 2.0, and start heating after the slurry is completely dispersed, at 2°C / Raise the temperature to 50°C at a rate of 1 minute, then operate at a constant temperature, drop in a solution formed by dissolving 20g sodium silicate nonahydrate and 10g NaOH in 200ml water, add liquid for 20 minutes, and the pH value will rise to 12.0. After 10 minutes, use a mass Adjust the pH value to 6.0 with dilute nitric acid with a fraction of 10%. After 10 minutes, filter and wash, add 10g of trisodium phosphate dodecahydrate and 5g of water to the filter cake, mix well and dry at 90°C. The dried filter cake is crushed and ground into powder, and recorded as sample 2.
PUM
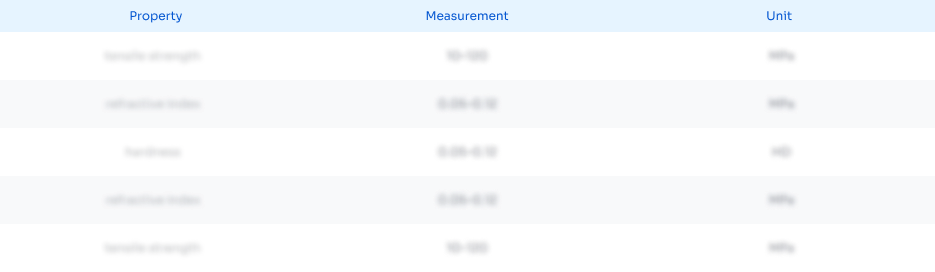
Abstract
Description
Claims
Application Information

- R&D
- Intellectual Property
- Life Sciences
- Materials
- Tech Scout
- Unparalleled Data Quality
- Higher Quality Content
- 60% Fewer Hallucinations
Browse by: Latest US Patents, China's latest patents, Technical Efficacy Thesaurus, Application Domain, Technology Topic, Popular Technical Reports.
© 2025 PatSnap. All rights reserved.Legal|Privacy policy|Modern Slavery Act Transparency Statement|Sitemap|About US| Contact US: help@patsnap.com