Process for manufacturing titanium anode by once oxidation
A titanium anode and process technology, applied in the field of preparation of coated electrodes, can solve the problems of wasting electric energy and manpower, cumbersome steps, etc., and achieve the effect of reducing production costs
- Summary
- Abstract
- Description
- Claims
- Application Information
AI Technical Summary
Problems solved by technology
Method used
Examples
Embodiment 1
[0045] A kind of primary oxidation manufacture titanium anode process, its operation method comprises the steps:
[0046] 1) The titanium plate is dried after mechanical processing, sand blasting, degreasing, pickling, and deionized water washing;
[0047] 2) Preparation of coating solution: add 50ml of ethanol and 50ml of isopropanol, and stir evenly with ultrasonic;
[0048] 3) Add 5 g of ethyl acetate as an additive to the solvent formed in step 2, and ultrasonically stir;
[0049] 4) Add 1g of chloroiridic acid, 1g of ruthenium trichloride, 1g of tantalum pentachloride and 1g of chloroplatinic acid to the solution formed in step 3, and stir evenly with ultrasound;
[0050] 5) Use the manual brush coating method to evenly coat the coating solution in step 4 on the titanium plate in step 1. After the solvent is naturally volatilized at room temperature until the surface is dry, enter the electric furnace at 500°C and oxidize at high temperature for 25 minutes. ;
[0051] ...
Embodiment 2
[0053] 1) The titanium plate is dried after mechanical processing, sand blasting, degreasing, pickling, and deionized water washing;
[0054] 2) Preparation of coating solution: add 50ml of ethanol and 50ml of isopropanol to form a mixed solvent, and stir evenly with ultrasonic;
[0055] 3) Add 5 g of ethyl acetate and 5 g of paraffin oil as additives to the solvent formed in step 2, and ultrasonically stir;
[0056] 4) Add 1g of chloroiridic acid, 1g of ruthenium trichloride, 1g of tantalum pentachloride and 1g of chloroplatinic acid to the solution formed in step 3, and stir evenly with ultrasound;
[0057] 5) Use the manual brush coating method to evenly coat the coating solution in step 4 on the titanium plate in step 1. After the solvent is naturally volatilized at room temperature until the surface is dry, enter the electric furnace at 500°C and oxidize at high temperature for 25 minutes. ;
[0058] 6) After the time is up, take it out from the electric furnace, and co...
Embodiment 3
[0060] 1) The titanium plate is dried after mechanical processing, sand blasting, degreasing, pickling, and deionized water washing;
[0061] 2) Coating liquid preparation: add 50ml n-butanol as solvent;
[0062] 3) Add 5 g of turpentine and 5 g of terpineol as additives to the solvent formed in step 2, and ultrasonically stir;
[0063] 4) Add 1g of chloroiridic acid, 1g of ruthenium trichloride, 1g of tantalum pentachloride and 1g of chloroplatinic acid to the solution formed in step 3, and stir evenly with ultrasound;
[0064] 5) Use the manual brush coating method to evenly coat the coating solution in step 4 on the titanium plate in step 1. After the solvent is naturally volatilized at room temperature until the surface is dry, enter the electric furnace at 500°C and oxidize at high temperature for 25 minutes. ;
[0065] 6) After the time is up, take it out from the electric furnace, and cool it to room temperature in the air, which is the titanium anode.
PUM
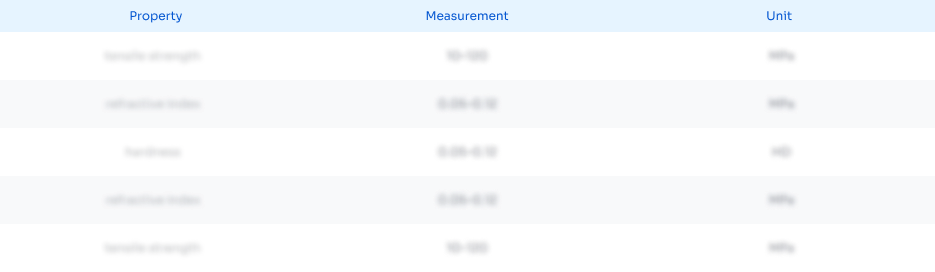
Abstract
Description
Claims
Application Information

- R&D Engineer
- R&D Manager
- IP Professional
- Industry Leading Data Capabilities
- Powerful AI technology
- Patent DNA Extraction
Browse by: Latest US Patents, China's latest patents, Technical Efficacy Thesaurus, Application Domain, Technology Topic, Popular Technical Reports.
© 2024 PatSnap. All rights reserved.Legal|Privacy policy|Modern Slavery Act Transparency Statement|Sitemap|About US| Contact US: help@patsnap.com