Method for separating lignin from agricultural waste by using composite ionic liquid
A technology of agricultural waste and compound ions, which is applied in the field of environmental protection, can solve the problems of cumbersome operation, many intermediate steps, and large dosage, and achieve the effect of simple conversion process, reduced dosage, and reduced dosage
- Summary
- Abstract
- Description
- Claims
- Application Information
AI Technical Summary
Problems solved by technology
Method used
Examples
Embodiment 1
[0031] A method for efficiently separating lignin from agricultural waste by using a composite ionic liquid system, the operation steps are as follows:
[0032] (1) Preparation of composite ionic liquid: 5g ionic liquid solvent 1-butyl-3-methylimidazolium chloride (bmimCl) and 0.1mol acidic ionic liquid catalyst 1-butanesulfonic acid group-3-methylimidazolium hydrogen sulfate Salt (C 4 h 8 SO 3 HmimHSO 4 ) at N 2 Fully mixed in an ice-water bath under protection to obtain a composite ionic liquid;
[0033] (2) Pretreatment of agricultural waste: After the bagasse is fully dried, it is crushed to 20-60 meshes by mechanical crushing. And wash its organic and water-soluble components with acetone and deionized water successively, and then fully dry it for later use;
[0034] (3) delignification of agricultural waste: 20g of the compound ionic liquid gained in step (1) is fully mixed with 1.5g bagasse, and the reaction system is subjected to N 2 After 3 replacements, heat t...
Embodiment 2
[0036] The difference between this embodiment and embodiment 1 is:
[0037] (1) Preparation of composite ionic liquid: 50g ionic liquid solvent 1-butyl-3-methylimidazole acetate (bmimAc) and 1mol acidic ionic liquid catalyst 1-butyl-3-methylimidazole hydrogen sulfate ( bmimHSO 4 ) at N 2 Fully mixed in an ice-water bath under protection to obtain a composite ionic liquid;
[0038] (3) Delignification of agricultural waste: 100g of the above-mentioned composite ionic liquid and 20g of rice husk were fully mixed, and the reaction system was subjected to N 2 After 3 replacements, heat to 200°C and react for 30 minutes under stirring conditions (speed 500r / min). After the reaction, cool the reactor to room temperature, pour out the contents of the reactor, fully dilute with 400mL of water, and filter. The solid obtained in the experiment After drying, the test showed that the lignin content in the solid matter was as high as 61.4%. The conversion rate of cellulose and hemicell...
Embodiment 3
[0040] The difference between this embodiment and embodiment 1 is:
[0041] (1) Preparation of composite ionic liquid: 200g of ionic liquid solvent 1-ethyl-3-methylimidazolium methyl sulfate (emimMeSO 4 ) and 5mol acidic ionic liquid catalyst 1-butanesulfonic acid pyridine bisulfate (C 4 h 8 SO 3 HSO 4 ) at N 2 Fully mixed in an ice-water bath under protection to obtain a composite ionic liquid;
[0042] (3) Delignification of agricultural waste: 500g of the above-mentioned composite ionic liquid and 60g of wheat straw were fully mixed, and the reaction system was subjected to N 2 After 3 replacements, heat to 240°C and react for 5 minutes under stirring conditions (speed 1000r / min). After the reaction, cool the reactor to room temperature, pour out the contents of the reactor, fully dilute with 500mL of water, and filter. The solid obtained in the experiment The content of lignin in the material is as high as 65.2%; almost 100% of cellulose and hemicellulose are convert...
PUM
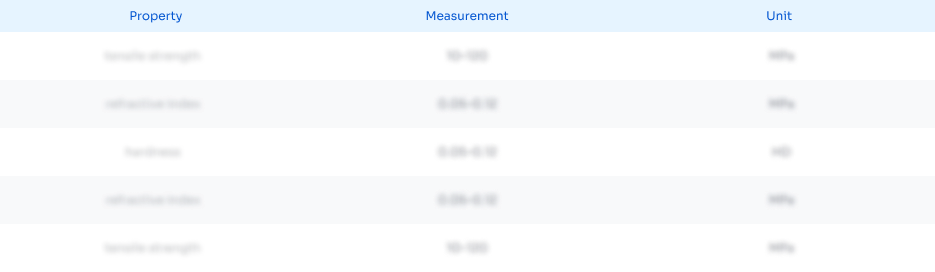
Abstract
Description
Claims
Application Information

- R&D
- Intellectual Property
- Life Sciences
- Materials
- Tech Scout
- Unparalleled Data Quality
- Higher Quality Content
- 60% Fewer Hallucinations
Browse by: Latest US Patents, China's latest patents, Technical Efficacy Thesaurus, Application Domain, Technology Topic, Popular Technical Reports.
© 2025 PatSnap. All rights reserved.Legal|Privacy policy|Modern Slavery Act Transparency Statement|Sitemap|About US| Contact US: help@patsnap.com