Method and device for preparing high-purity low-metallic impurity tantalum chloride through one-step process
A technology of tantalum pentachloride and low metal, applied in the field of rare metal powder material preparation, can solve the problems of high content of metal impurities and oxychloride, cumbersome process, etc., and achieve the effects of high purity, simple process and short process flow
- Summary
- Abstract
- Description
- Claims
- Application Information
AI Technical Summary
Problems solved by technology
Method used
Image
Examples
Embodiment 1
[0027] The device used in the present invention is as figure 1 As shown, the device consists of four parts: a vertical chlorination furnace 1, a collection tower 2, a vacuum system 3 and a tail gas absorption system 4. Wherein the top of the chlorination furnace 1 is set as a tantalum source feeding port 11, the side bottom is provided with a gas source inlet 13, and the bottom is an ash outlet 14; there is a buffer electric heating belt 15 between the vertical chlorination furnace 1 and the collecting tower 2 , with enough resistance wires to ensure that the temperature of the buffer zone is 300~600°C; the collection tower 2 is composed of an air cooling system 21 at the top 1 / 3 and a water cooling system at the middle 2 / 3, and the bottom of the collection tower 2 is equipped with a finished product A discharge port 23; in addition, a vacuum system 3 is provided at the side of the collection tower near the top 1 / 6, and a tail gas absorption system 4 is provided at the side ne...
Embodiment 2
[0031] Use 1 / 2 tantalum chips and 1 / 2 tantalum powder as the tantalum source, put the tantalum source into the chlorination furnace, control the system vacuum to 0.03Mpa, add inert gas argon with a purity of 99.99%, and react Hydrogen gas with a purity of 99.9% was introduced to hydrogenate the tantalum source, and the hydrogen gas was replaced with inert gas argon for 90 minutes. After the replacement, chlorine gas was introduced to react, and the temperature of the chlorination furnace was controlled at 400°C. The purity of chlorine gas is 99.9%. The molar ratio of tantalum source and chlorine gas is 200:650; the molar ratio of tantalum source:hydrogen gas is 200:200, and the volume of the receiving tower is three times that of the chlorination furnace. The finished tantalum products are analyzed in the following table:
[0032]
Embodiment 3
[0034] Use 1 / 2 tantalum rod and 1 / 2 tantalum block as the tantalum source, put the tantalum source into the chlorination furnace, control the system vacuum to 0.01Mpa, add inert gas argon with a purity of 99.99%, and react The hydrogen gas with a purity of 99.9% was introduced to hydrogenate the tantalum source, and then the hydrogen gas was replaced with an inert gas argon for 120 minutes. After the replacement, chlorine gas was introduced to react, and the temperature of the chlorination furnace was controlled at 400°C. The purity of chlorine gas is 99.9%. The molar ratio of tantalum source and chlorine gas is 200:700; the molar ratio of tantalum source:hydrogen gas is 200:300, and the volume of the receiving tower is 1.5 times that of the chlorination furnace. After 12 hours of reaction, the finished product of tantalum pentachloride is collected and analyzed. As shown in the following table:
[0035]
PUM
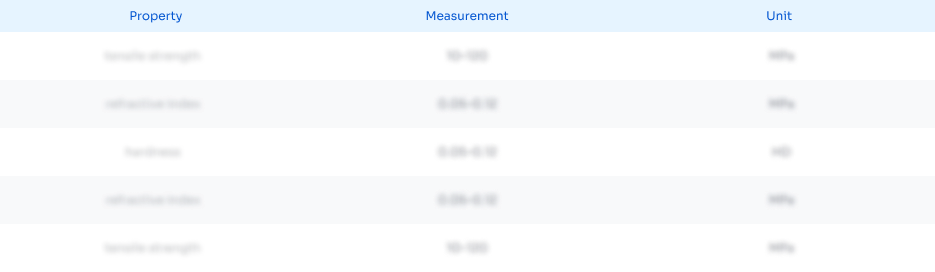
Abstract
Description
Claims
Application Information

- R&D Engineer
- R&D Manager
- IP Professional
- Industry Leading Data Capabilities
- Powerful AI technology
- Patent DNA Extraction
Browse by: Latest US Patents, China's latest patents, Technical Efficacy Thesaurus, Application Domain, Technology Topic, Popular Technical Reports.
© 2024 PatSnap. All rights reserved.Legal|Privacy policy|Modern Slavery Act Transparency Statement|Sitemap|About US| Contact US: help@patsnap.com