Waste and old tire colloidal particle cracking system and method
A waste tire rubber and pyrolysis system technology, applied in the field of tire recycling, can solve the problems of nowhere to release pyrolysis heat, ineffective use of heat energy, heat waste, etc., so as to improve pyrolysis operation conditions, improve material heating efficiency, and improve combustion. effect of effect
- Summary
- Abstract
- Description
- Claims
- Application Information
AI Technical Summary
Problems solved by technology
Method used
Image
Examples
Embodiment Construction
[0032] The preferred embodiments of the present invention will be described in detail below in conjunction with the accompanying drawings, so that the advantages and features of the present invention can be more easily understood by those skilled in the art, so as to define the protection scope of the present invention more clearly.
[0033] refer to figure 1 As shown, a kind of waste tire colloid pyrolysis system provided by the present invention comprises conveying device 1, and crushing device 2, washing device 3, drying device 4, cracking furnace 5 are sequentially connected on conveying device 1, and crushing device 2 is also connected with The feeding device 6 is connected, and the cracking furnace 5 is also connected with the molten salt furnace 8 through the salt inlet pipe 7, and the molten salt furnace 8 is connected with the drying device 4 through the transition salt pipe 9, and the gas inlet pipe 10 is installed on the molten salt furnace 8, The drying device 4 is...
PUM
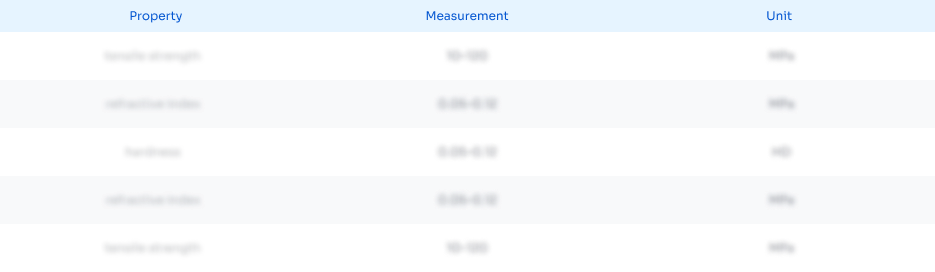
Abstract
Description
Claims
Application Information

- R&D Engineer
- R&D Manager
- IP Professional
- Industry Leading Data Capabilities
- Powerful AI technology
- Patent DNA Extraction
Browse by: Latest US Patents, China's latest patents, Technical Efficacy Thesaurus, Application Domain, Technology Topic, Popular Technical Reports.
© 2024 PatSnap. All rights reserved.Legal|Privacy policy|Modern Slavery Act Transparency Statement|Sitemap|About US| Contact US: help@patsnap.com