Ceramic grouting equipment with automatic feeding function and grouting method
An automatic feeding and grouting technology, which is applied to ceramic molding machines, ceramic molding workshops, auxiliary molding equipment, etc., can solve the problems of easy blockage of pipelines, low labor efficiency, and inability to adjust, so as to improve the quality of green bodies and reduce operations. Strength, the effect of improving the utilization rate
- Summary
- Abstract
- Description
- Claims
- Application Information
AI Technical Summary
Problems solved by technology
Method used
Image
Examples
specific Embodiment 1
[0028] Specific embodiment one: with reference to figure 1 As shown, automatic feeding ceramic grouting equipment, including feeding system, grouting system, operating platform and waste recycling system;
[0029] The feeding system includes a slurry mixing tank 11, a feeding pipeline 12 and a booster pump 13. The mixing tank 11 is located above the feeding track or the slurry mixing tank 11 is placed on a higher floor. The feeding pipeline 12 includes a main A feed pipeline 121 and a plurality of distribution pipelines 122, the two ends of the main feed pipeline 121 are respectively communicated with the slurry mixing cylinder 11 and the booster pump 13, and the distribution pipelines 122 are respectively communicated with the booster pump 13;
[0030] The grouting system includes a frame 21, a plurality of slide rails 22 and a grouting device 23. The frame 21 is provided with a pipe distribution channel 211 for fixing the distribution pipe 122, and the distribution pipe 122 ...
specific Embodiment 2
[0038] Specific embodiment two: as figure 2 As shown, the operating platform is single, and other components and structures are the same as those in Embodiment 1.
specific Embodiment 3
[0039] Specific embodiment three: as image 3 As shown, the waste collection bucket 41 is located directly below the frame 21, and other components and structures are the same as those in the first embodiment.
PUM
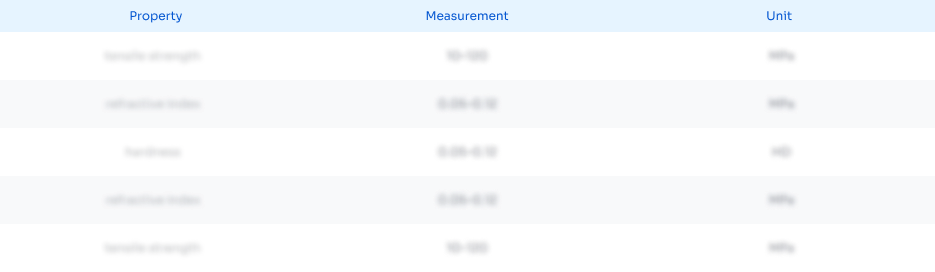
Abstract
Description
Claims
Application Information

- R&D Engineer
- R&D Manager
- IP Professional
- Industry Leading Data Capabilities
- Powerful AI technology
- Patent DNA Extraction
Browse by: Latest US Patents, China's latest patents, Technical Efficacy Thesaurus, Application Domain, Technology Topic, Popular Technical Reports.
© 2024 PatSnap. All rights reserved.Legal|Privacy policy|Modern Slavery Act Transparency Statement|Sitemap|About US| Contact US: help@patsnap.com