Method and device for automatic finish machining of thin-walled pipe orifices
A technology for thin-walled tubes and nozzles, which is applied in the field of automatic thin-walled tube nozzle finishing devices, which can solve problems such as nozzle deformation and achieve good machining accuracy.
- Summary
- Abstract
- Description
- Claims
- Application Information
AI Technical Summary
Problems solved by technology
Method used
Image
Examples
Embodiment Construction
[0042] The transmission transport assembly 10 is installed on the top plate and the middle beam of the bed 2 of the conveying finishing device, the motor movement assembly 1 and the motor movement assembly 2 9 are respectively installed on the top plate of the bed 2 of the conveying finishing device, and the automatic push rod Component 1 3 and automatic push rod component 2 6 are installed opposite to each other on both sides of the automatic feeding and positioning component 4, and are fixed on the top plate of the bed 5 of the automatic lining device through screws, and the bed 2 of the conveying finishing device passes through The plate 7 is connected with the bed 5 of the automatic lining device, and the two conveying chains and the fixture assembly 8 are respectively installed on the bed 2 of the conveying finishing device through the conveying sprockets of the transmission conveying assembly, and the discharge plate 11 is installed on the conveying type The side of the b...
PUM
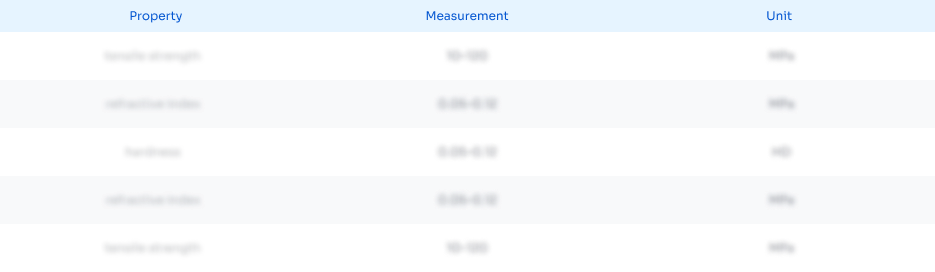
Abstract
Description
Claims
Application Information

- R&D Engineer
- R&D Manager
- IP Professional
- Industry Leading Data Capabilities
- Powerful AI technology
- Patent DNA Extraction
Browse by: Latest US Patents, China's latest patents, Technical Efficacy Thesaurus, Application Domain, Technology Topic, Popular Technical Reports.
© 2024 PatSnap. All rights reserved.Legal|Privacy policy|Modern Slavery Act Transparency Statement|Sitemap|About US| Contact US: help@patsnap.com