Multi-tank type sensible heat recovery device and method for sintered ore
A sensible heat recovery and sintering technology, applied in waste heat treatment, lighting and heating equipment, furnaces, etc., can solve the problems of high energy consumption, high concentration, and limited gas temperature rise in vertical tanks, and achieve high-grade waste heat recovery and hot ore Uniform particle size and reduced heat loss
- Summary
- Abstract
- Description
- Claims
- Application Information
AI Technical Summary
Problems solved by technology
Method used
Image
Examples
Embodiment
[0085] The sintering machine area is 600m 2 , a sinter production line with an hourly sinter output of about 810 tons is taken as an example. The original sinter adopts a ring cooler as shown in Table 1, and a total of 5 cooling fans are installed, and the design air volume of a single fan is 66.51m 3 / h. The red-hot sintered ore falls into the ore bin through the tail end of the sintering trolley and enters the ring cooler. Under the action of 5 cooling fans, the hot ore is reduced from 600 to 800°C to below 150°C and sent to the blast furnace through the conveyor belt. Utilization, the waste heat obtained from the ring cooler is led to the waste heat boiler to produce low-pressure steam and reused on the grid. Due to the low temperature of the ring cooling waste gas, the actual waste heat recovery rate is only 20-30%.
[0086] Now adopted a kind of multi-tank sensible heat recovery device and sensible heat recovery method for sintering ore of the present invention, it is sp...
PUM
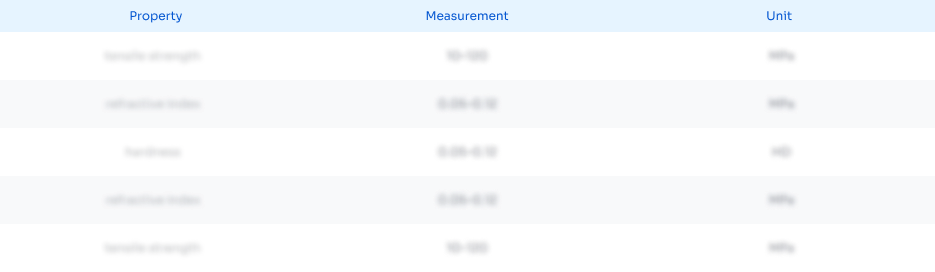
Abstract
Description
Claims
Application Information

- Generate Ideas
- Intellectual Property
- Life Sciences
- Materials
- Tech Scout
- Unparalleled Data Quality
- Higher Quality Content
- 60% Fewer Hallucinations
Browse by: Latest US Patents, China's latest patents, Technical Efficacy Thesaurus, Application Domain, Technology Topic, Popular Technical Reports.
© 2025 PatSnap. All rights reserved.Legal|Privacy policy|Modern Slavery Act Transparency Statement|Sitemap|About US| Contact US: help@patsnap.com