Fibrilia enhanced polyurethane composite board and preparation method thereof
A fiber composite board and hemp fiber technology, which is applied in the field of automobile material design and manufacture, can solve problems such as insufficient mechanical properties of the hemp fiber composite board, and achieve the effects of good application prospect, good environmental protection performance and light weight.
- Summary
- Abstract
- Description
- Claims
- Application Information
AI Technical Summary
Problems solved by technology
Method used
Image
Examples
Embodiment 1
[0022] In the present embodiment, the preparation method of hemp fiber reinforced polyurethane composite board is as follows:
[0023] Step 1, laying finely opened hemp fiber felt on the hemp fiber composite board;
[0024] Step 2: Spray polyurethane on the hemp fiber felt to obtain a core layer; the polyurethane is made of rigid polyurethane foam material, and the mass ratio of hemp fiber to polyurethane is: 30% of hemp fiber and 70% of polyurethane.
[0025] Step 3, laying a layer of hemp fiber composite board on the core layer;
[0026] Step 4, then hot pressing at 120°C to 140°C and a pressure of 0.5 to 5 MPa for 30 to 100 seconds.
[0027] Step 5, after cooling, the hemp fiber reinforced polyurethane composite board is obtained.
[0028] Step 6: Cutting the hemp fiber reinforced polyurethane composite board to obtain hemp fiber reinforced polyurethane composite boards of the same size.
[0029] The structure of the obtained hemp fiber reinforced polyurethane composite ...
Embodiment 2
[0032] Step 1, laying finely opened hemp fiber felt on the hemp fiber composite board;
[0033] Step 2: Spray polyurethane on the hemp fiber felt to obtain a core layer; the polyurethane is made of rigid polyurethane foam material, and the mass ratio of hemp fiber to polyurethane is: hemp fiber 40%, polyurethane 60%.
[0034] Step 3, laying a layer of hemp fiber composite board on the core layer;
[0035] Step 4, then hot pressing at 120°C to 140°C and a pressure of 0.5 to 5 MPa for 30 to 100 seconds.
[0036] Step 5, after cooling, the hemp fiber reinforced polyurethane composite board is obtained.
[0037] Step 6: Cutting the hemp fiber reinforced polyurethane composite board to obtain hemp fiber reinforced polyurethane composite boards of the same size.
Embodiment 3
[0039] Step 1, laying finely opened hemp fiber felt on the hemp fiber composite board;
[0040] Step 2: Spray polyurethane on the hemp fiber felt to obtain a core layer; the polyurethane is made of rigid polyurethane foam material, and the mass ratio of hemp fiber to polyurethane is: hemp fiber 50%, polyurethane 50%.
[0041] Step 3, laying a layer of hemp fiber composite board on the core layer;
[0042] Step 4, then hot pressing at 120°C to 140°C and a pressure of 0.5 to 5 MPa for 30 to 100 seconds.
[0043] Step 5, after cooling, the hemp fiber reinforced polyurethane composite board is obtained.
[0044] Step 6: Cutting the hemp fiber reinforced polyurethane composite board to obtain hemp fiber reinforced polyurethane composite boards of the same size.
[0045] The finely opened hemp fiber felt of the above embodiments is obtained through fine opening of hemp fibers of 80 to 100 mm.
[0046] Effect verification
[0047] According to the content of filling hemp fiber, t...
PUM
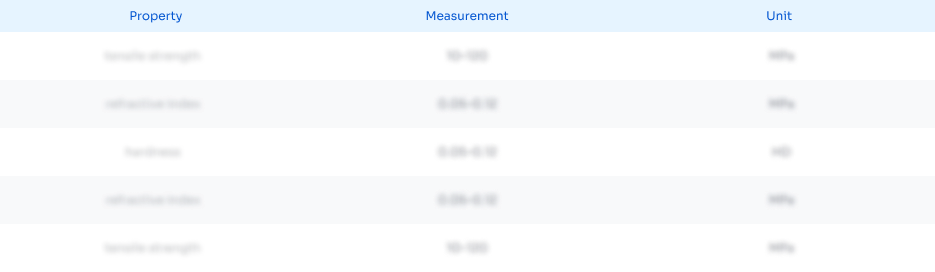
Abstract
Description
Claims
Application Information

- R&D
- Intellectual Property
- Life Sciences
- Materials
- Tech Scout
- Unparalleled Data Quality
- Higher Quality Content
- 60% Fewer Hallucinations
Browse by: Latest US Patents, China's latest patents, Technical Efficacy Thesaurus, Application Domain, Technology Topic, Popular Technical Reports.
© 2025 PatSnap. All rights reserved.Legal|Privacy policy|Modern Slavery Act Transparency Statement|Sitemap|About US| Contact US: help@patsnap.com