Preparation method of silicon oxide layer for solar cell and solar cell
A technology for solar cells and silicon oxide layers, applied in the field of solar cells, can solve the problems of low content of high-valence silicon, difficult to control thickness, small thickness of silicon oxide layer, etc. Effect
- Summary
- Abstract
- Description
- Claims
- Application Information
AI Technical Summary
Problems solved by technology
Method used
Image
Examples
Embodiment 1
[0055] The oriented n-type silicon wafer is pretreated, that is, the silicon wafer is first cleaned by RCA standard cleaning method, and then the native oxide layer on the surface of the silicon wafer is removed by HF; the pretreated silicon wafer is placed in a temperature of 20°C Oxidation treatment for 2 minutes in the mixed acid solution, wherein the mixed acid solution is formed by mixing nitric acid (68%) and sulfuric acid (98%) at a volume ratio of 3:1.
[0056] The thickness of the silicon oxide layer was measured to be 1.2 nm by spectroscopic ellipsometry.
Embodiment 2
[0058] The oriented n-type silicon wafer is pretreated, that is, the silicon wafer is first cleaned by RCA standard cleaning method, and then the original oxide layer on the surface of the silicon wafer is removed by HF; the pretreated silicon wafer is placed in a temperature of 120 ° C Oxidation treatment in the mixed acid solution for 10 minutes, wherein the mixed acid solution is formed by mixing nitric acid (68%) and sulfuric acid (98%) at a volume ratio of 9:1.
[0059] The thickness of the silicon oxide layer was measured by spectroscopic ellipsometry to be 2.3 nm.
Embodiment 3
[0061] Pretreat the oriented n-type silicon wafer, that is, the silicon wafer is first cleaned by RCA standard cleaning method, and then the native oxide layer on the surface of the silicon wafer is removed by HF; the pretreated silicon wafer is placed in a temperature of 90 ° C Oxidation treatment in the mixed acid solution for 10 minutes, wherein the mixed acid solution is formed by mixing nitric acid (68%) and sulfuric acid (98%) at a volume ratio of 1:1.
[0062] The thickness of the silicon oxide layer was measured to be 2.0 nm by spectroscopic ellipsometry.
PUM
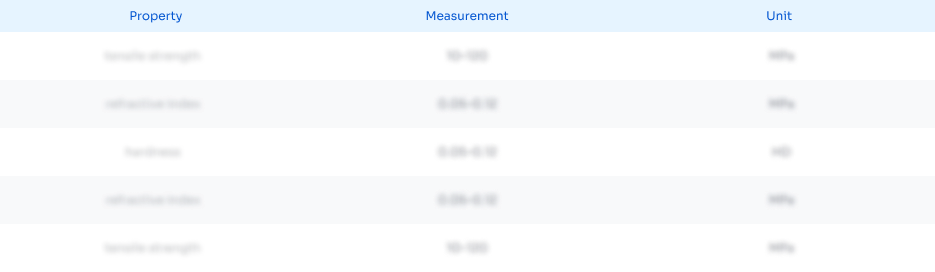
Abstract
Description
Claims
Application Information

- R&D Engineer
- R&D Manager
- IP Professional
- Industry Leading Data Capabilities
- Powerful AI technology
- Patent DNA Extraction
Browse by: Latest US Patents, China's latest patents, Technical Efficacy Thesaurus, Application Domain, Technology Topic, Popular Technical Reports.
© 2024 PatSnap. All rights reserved.Legal|Privacy policy|Modern Slavery Act Transparency Statement|Sitemap|About US| Contact US: help@patsnap.com