Smelting method of ultralow-oxygen and medium-high-carbon steel
A smelting method and medium and high carbon technology, applied in the smelting field of ultra-low oxygen medium and high carbon steel, can solve the problems of increased metal loss and temperature loss, long refining treatment period, difficult production organization, etc., so as to reduce desulfurization pressure and promote full floating The effect of eliminating and shortening the processing time
- Summary
- Abstract
- Description
- Claims
- Application Information
AI Technical Summary
Problems solved by technology
Method used
Image
Examples
Embodiment 1
[0018] Example 1: A method for smelting ultra-low oxygen medium-high carbon steel
[0019] Steel type: GCr15. The tapping amount is 140t, [C]= 0.95%~1.0%, [Mn] =0.25%~0.45%, [Cr] =1.3%~1.6%, the specific steps are as follows:
[0020] (1) Raw materials for the converter: Feed iron [S]=0.003%, special low-sulfur scrap steel is used, and the end point of the converter [S]=0.009%.
[0021] (2) End point control of the converter: end point [C] =0.2%; tapping temperature 1601°C, end point constant oxygen [O]=200ppm.
[0022] (3) Slag blocking for converter tapping: the thickness of the ladle slag layer is 35mm.
[0023] (4) Converter carbon powder addition: 460kg of carbon powder is added before tapping, and 380kg is added within 2 to 4 minutes of tapping.
[0024] (5) Stirring of molten steel for tapping: within 4 minutes from the start of tapping, the flow rate of bottom blowing argon is controlled at 300Nl / min; from 4 min to the end of tapping, the bottom blowing argon is tur...
Embodiment 2
[0029] Example 2: A method for smelting ultra-low oxygen medium-high carbon steel
[0030] Steel type: GCr15. The tapping amount is 142t, [C]= 0.18%~0.2%, [Mn]= 0.9%~1.0%, [Cr]= 1.1%~1.2%, the specific steps are:
[0031] (1) Raw materials for the converter: Feed iron [S]=0.002%, special low-sulfur scrap steel is used, and the end point of the converter [S]=0.009%.
[0032] (2) End point control of converter: end point [C] =0.12%; tapping temperature 1620°C, end point constant oxygen [O]=260ppm.
[0033] (3) Slag blocking for converter tapping: the thickness of the ladle slag layer is 38mm.
[0034] (4) Converter carbon powder addition: 90kg of carbon powder is added before tapping, and 70kg of carbon powder is added within 2 to 4 minutes of tapping.
[0035] (5) Stirring of molten steel for tapping: within 4 minutes from the start of tapping, the bottom blowing argon gas flow rate is controlled at 320Nl / min; from 4 min to the end of tapping, the bottom blowing argon gas is...
PUM
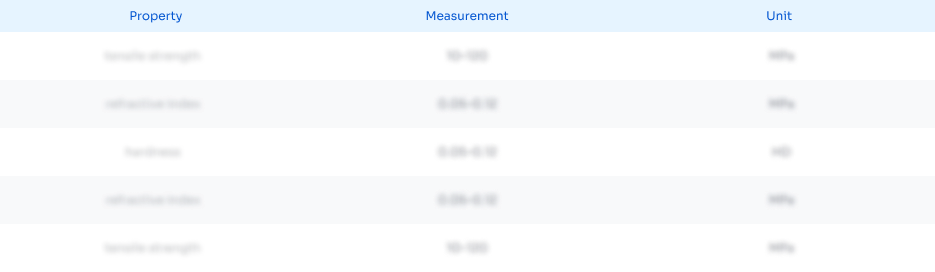
Abstract
Description
Claims
Application Information

- R&D Engineer
- R&D Manager
- IP Professional
- Industry Leading Data Capabilities
- Powerful AI technology
- Patent DNA Extraction
Browse by: Latest US Patents, China's latest patents, Technical Efficacy Thesaurus, Application Domain, Technology Topic, Popular Technical Reports.
© 2024 PatSnap. All rights reserved.Legal|Privacy policy|Modern Slavery Act Transparency Statement|Sitemap|About US| Contact US: help@patsnap.com