Method for removing iron and silicon impurities in silicon carbide micropowder for crystalline silicon wire cutting
A technology of silicon carbide micropowder and silicon carbide powder, applied in silicon carbide, carbide and other directions, can solve the problems of inability to play, remove, and consume large amounts of iron trioxide and silicon impurities, achieving a high degree of automation and improving utilization. efficiency, reducing material loss
- Summary
- Abstract
- Description
- Claims
- Application Information
AI Technical Summary
Problems solved by technology
Method used
Image
Examples
Embodiment 1
[0028] (1) Pulping: the particle size after grinding by Raymond mill is D 3 ≤14.8μm, D 94 ≥4.8μm silicon carbide micropowder and deionized water were mixed evenly for 30 minutes to prepare a silicon carbide micropowder slurry with a mass concentration of 25%;
[0029] (2) Dispersion treatment: add sodium pyrophosphate with a silicon carbide mass fraction of 0.6% to the uniform silicon carbide micropowder slurry prepared above, and stir evenly for 40 minutes;
[0030] (3) Electromagnetic iron removal: the silicon carbide micro-powder slurry obtained from the above dispersion is pumped at a distance of 4.5m 3 The / h flow rate is injected into the electromagnetic magnetic separator for iron removal, and the purified silicon carbide micro-powder slurry and the iron-rich silicon carbide micro-powder slurry are respectively obtained;
[0031] (4) Cleaning: Add deionized water to the purified silicon carbide micropowder slurry obtained after the above iron removal, stir evenly, let...
Embodiment 2
[0036] (1) Pulping: the particle size after grinding by Raymond mill is D 3 ≤14.8μm, D 94 ≥4.8μm silicon carbide micropowder and deionized water were uniformly stirred for 35 minutes and mixed to prepare a silicon carbide micropowder slurry with a mass concentration of 35%;
[0037] (2) Dispersion treatment: add sodium hexametaphosphate with a silicon carbide mass fraction of 0.5% to the uniform silicon carbide micropowder slurry prepared above, and stir evenly for 45 minutes;
[0038] (3) Electromagnetic iron removal: the silicon carbide micro-powder slurry obtained from the above dispersion is pumped at a distance of 4.5m 3 The / h flow rate is injected into the electromagnetic magnetic separator for iron removal, and the purified silicon carbide micro-powder slurry and the iron-rich silicon carbide micro-powder slurry are respectively obtained;
[0039] (4) Cleaning: add deionized water to the purified silicon carbide micropowder slurry obtained after the above iron remova...
PUM
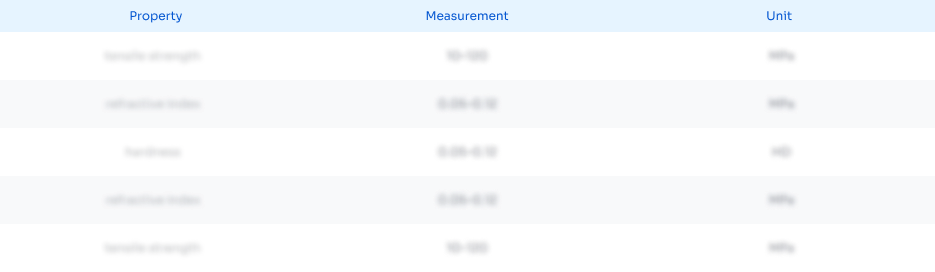
Abstract
Description
Claims
Application Information

- R&D
- Intellectual Property
- Life Sciences
- Materials
- Tech Scout
- Unparalleled Data Quality
- Higher Quality Content
- 60% Fewer Hallucinations
Browse by: Latest US Patents, China's latest patents, Technical Efficacy Thesaurus, Application Domain, Technology Topic, Popular Technical Reports.
© 2025 PatSnap. All rights reserved.Legal|Privacy policy|Modern Slavery Act Transparency Statement|Sitemap|About US| Contact US: help@patsnap.com