Aeroengine precision forging stator blade intake and exhaust edge CNC abrasive belt grinding tooling
A technology for aero-engines, intake and exhaust edges, applied to abrasive belt grinders, grinding workpiece supports, machine tools suitable for grinding workpiece edges, etc., can solve the problem that the curvature transition of the blade end cannot be processed normally and affect the intake and exhaust Grinding length of air edge, unreasonable structural design of positioning block, etc., to achieve compact structure, reduce the number of fixtures, and reduce processing costs
- Summary
- Abstract
- Description
- Claims
- Application Information
AI Technical Summary
Problems solved by technology
Method used
Image
Examples
Embodiment Construction
[0033] The present invention will be further described below in conjunction with accompanying drawing,
[0034] Such as figure 1 yes Figure 8 As shown, the aeroengine precision forging stator blade inlet and exhaust edge numerical control abrasive belt grinding tooling of the present invention includes a clamp 20110 for clamping the process boss 30-1 at both ends of the blade 30, and is used for adjusting the blade surface 30-1. 2 Positioning the profile positioning block 20109 and the clamp base 5200, the profile positioning block 20109 is arranged on the clamp base 5200;
[0035]The fixture base 5200 includes a base plate 1, a support 8 is provided on the base plate 1, a vertical linear guide rail 11 is provided on the support 8, a groove 8-2 is opened on the support 8, and the linear guide rail 11 is arranged in the groove 8-2. There is also a pressure block 9 in the groove 8-2, one side of the linear guide rail 11 is close to one side of the groove 8-2, and the pressure...
PUM
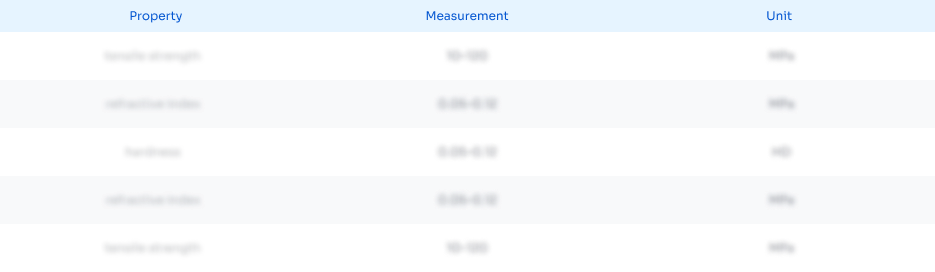
Abstract
Description
Claims
Application Information

- Generate Ideas
- Intellectual Property
- Life Sciences
- Materials
- Tech Scout
- Unparalleled Data Quality
- Higher Quality Content
- 60% Fewer Hallucinations
Browse by: Latest US Patents, China's latest patents, Technical Efficacy Thesaurus, Application Domain, Technology Topic, Popular Technical Reports.
© 2025 PatSnap. All rights reserved.Legal|Privacy policy|Modern Slavery Act Transparency Statement|Sitemap|About US| Contact US: help@patsnap.com