Combined manufacturing method of titanium alloy curvature component with ribs
A technology of titanium alloy with ribs and titanium alloy with ribs, which is applied in the field of metal forming, can solve the problems of poor forming accuracy, high manufacturing cost, and low material utilization rate, and achieve the effects of shortening the manufacturing cycle, improving production efficiency, and saving tooling costs
- Summary
- Abstract
- Description
- Claims
- Application Information
AI Technical Summary
Problems solved by technology
Method used
Image
Examples
Embodiment Construction
[0036] In the following, with reference to the accompanying drawings and specific examples, the specific implementation manners adopted by the present invention to achieve the predetermined invention objectives will be further described.
[0037] figure 1 It is a flow chart of an embodiment of a combined manufacturing method of a ribbed titanium alloy curvature member of the present invention. like figure 1 As shown, the process includes:
[0038] Step 1. Using additive manufacturing technology (including but not limited to laser melting deposition, electron beam fuse deposition), in the predetermined area on the titanium alloy straight profile with equal cross-section, add material to manufacture local reinforcing ribs to form a straight titanium alloy with ribs. profiles;
[0039] Step 2. Using profile hot stretch bending forming technology, carry out self-resistance heating and stretching of the ribbed titanium alloy straight profile to form the required curvature shape,...
PUM
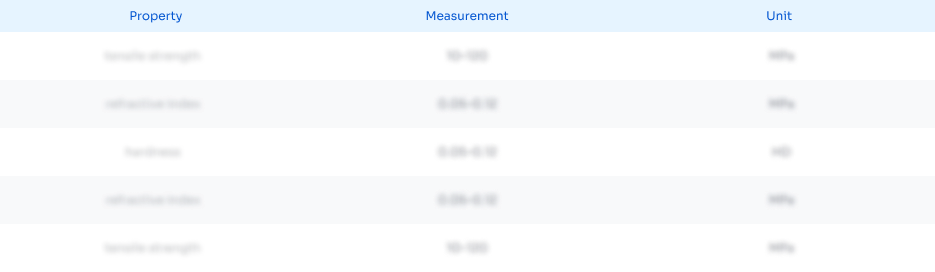
Abstract
Description
Claims
Application Information

- R&D Engineer
- R&D Manager
- IP Professional
- Industry Leading Data Capabilities
- Powerful AI technology
- Patent DNA Extraction
Browse by: Latest US Patents, China's latest patents, Technical Efficacy Thesaurus, Application Domain, Technology Topic, Popular Technical Reports.
© 2024 PatSnap. All rights reserved.Legal|Privacy policy|Modern Slavery Act Transparency Statement|Sitemap|About US| Contact US: help@patsnap.com