Inner by-pass valve type magnetorheological fluid suspension
A magnetorheological fluid and channel technology, applied in springs, shock absorbers, springs/shock absorbers, etc., can solve the problems of increasing the zero-field dynamic stiffness of the suspension, increasing the production cost, and the large volume of the upper liquid chamber. Achieve the effect of reducing the zero-field dynamic stiffness of the mount, the large-zero field dynamic stiffness, and the simple structure of the piston
- Summary
- Abstract
- Description
- Claims
- Application Information
AI Technical Summary
Problems solved by technology
Method used
Image
Examples
Embodiment Construction
[0032] see Figure 1a , Figure 1b , Figure 2a and Figure 2b , the structural form of the inner bypass channel valve magneto-rheological fluid mount in this embodiment is:
[0033] The magnetorheological fluid unit is set to realize damping control. The upper end cover 6 and the lower end cover 15 are arranged one by one at the upper and lower ends of the outer cylinder body 4 to form a closed hydraulic chamber with constant volume, and the hydraulic chamber is filled with magnetorheological fluid. Liquid; the inner cylinder 20 is concentrically arranged in the outer cylinder 4, and an annular flow channel is formed between the inner side wall of the outer cylinder 4 and the outer side wall of the inner cylinder 20; between the top end surface of the inner cylinder 20 and the upper end cover 6 A plurality of upper isolation blocks 7 are arranged at intervals along the circumference, and a plurality of lower isolation blocks 17 are arranged at intervals along the circumferenc...
PUM
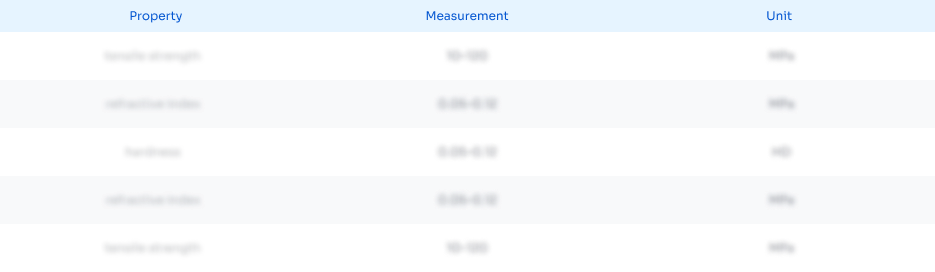
Abstract
Description
Claims
Application Information

- Generate Ideas
- Intellectual Property
- Life Sciences
- Materials
- Tech Scout
- Unparalleled Data Quality
- Higher Quality Content
- 60% Fewer Hallucinations
Browse by: Latest US Patents, China's latest patents, Technical Efficacy Thesaurus, Application Domain, Technology Topic, Popular Technical Reports.
© 2025 PatSnap. All rights reserved.Legal|Privacy policy|Modern Slavery Act Transparency Statement|Sitemap|About US| Contact US: help@patsnap.com