Liquid die forging process of a357 aluminum alloy applied to commercial vehicle axle heads
A technology of A357 and liquid die forging, which is applied in the field of liquid die forging process of A357 aluminum alloy, can solve the problems of no application of rare earth elements, etc., achieve obvious economic and social benefits, improve the appearance quality, and increase the tensile strength.
- Summary
- Abstract
- Description
- Claims
- Application Information
AI Technical Summary
Problems solved by technology
Method used
Image
Examples
Embodiment 1
[0037](1) Alloy composition optimization: optimize the ratio of Mg / Si and other alloy elements in A357 aluminum alloy, and control the mass content of impurity elements, including Si7 parts; Fe<0.1 parts; Cu<0.1 parts; Mg0.6 parts; 0.02 parts of Sr; 0.2 parts of Ti; 95 parts of Al, control the other individual impurities in A357 aluminum alloy to ≤0.04 parts, then add 0.3 parts of Gd; 0.5 parts of Sm; 1 part of Hf, use Sr and Ti for modification and refinement treatment; In this step, it is necessary to strictly control the amount of Gd and Sm added, because adding too much will not only not improve the performance of the aluminum alloy, but also affect the normal use of the aluminum alloy, and even cause the scrap of the material;
[0038] (2) Melting;
[0039] (3) The melt obtained in step (2) is degassed and slag-removed in the furnace with a high-efficiency refining agent to make the melt clean and free of impurities; removing impurities and gases inside the aluminum alloy...
Embodiment 2
[0051] (1) Alloy composition optimization: optimize the Mg / Si ratio and the ratio of other alloying elements in the A357 aluminum alloy, and control the mass content of impurity elements, of which Si6.5 parts; Fe<0.2 parts; Cu<0.2 parts; Mg0.5 0.01 parts of Sr; 0.15 parts of Ti; 90 parts of Al, control other single impurities in A357 aluminum alloy to ≤0.05 parts, then add elements Gd0.1 part; Sm0.1 part; Hf0.1 part, use Sr and Ti as modification and refinement;
[0052] (2) Melting;
[0053] (3) The melt obtained in step (2) is degassed and slag-removed in the furnace with a high-efficiency refining agent to make the melt clean and free of impurities;
[0054] (4) Liquid die forging is divided into 5 stages
[0055] The first stage: the melt is poured into the shaft head mold: the pouring temperature is 680°C, the mold preheating temperature is 320°C, and the single billet is poured accurately and quantitatively;
[0056] The second stage: fast filling: the pressurization ...
Embodiment 3
[0064] (1) Alloy composition optimization: optimize the ratio of Mg / Si and other alloy elements in the A357 aluminum alloy, and control the mass content of impurity elements, including Si7.5 parts; Fe<0.15 parts; Cu<0.15 parts; Mg0.6 0.015 parts of Sr; 0.1 parts of Ti; 93 parts of Al, control the other individual impurities in A357 aluminum alloy to ≤0.03 parts, then add 0.5 parts of Gd; 0.5 parts of Sm; treatment;
[0065] (2) Melting;
[0066] (3) The melt obtained in step (2) is degassed and slag-removed in the furnace with a high-efficiency refining agent to make the melt clean and free of impurities;
[0067] (4) Liquid die forging is divided into 5 stages
[0068] The first stage: the melt is poured into the shaft head mold: the pouring temperature is 680°C, the mold preheating temperature is 280°C, and the single billet is poured accurately and quantitatively;
[0069] The second stage: fast filling: the pressurization time of mold closing is 15 seconds, and the pres...
PUM
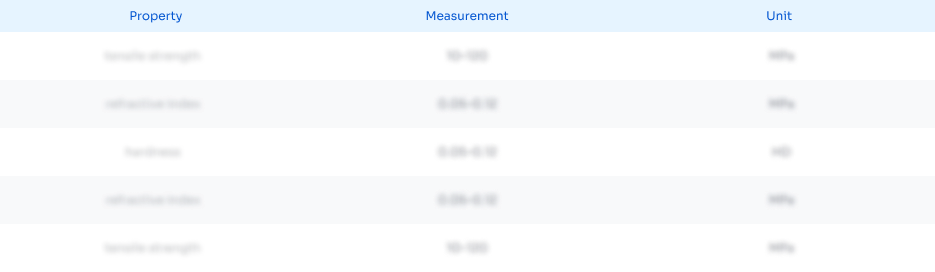
Abstract
Description
Claims
Application Information

- Generate Ideas
- Intellectual Property
- Life Sciences
- Materials
- Tech Scout
- Unparalleled Data Quality
- Higher Quality Content
- 60% Fewer Hallucinations
Browse by: Latest US Patents, China's latest patents, Technical Efficacy Thesaurus, Application Domain, Technology Topic, Popular Technical Reports.
© 2025 PatSnap. All rights reserved.Legal|Privacy policy|Modern Slavery Act Transparency Statement|Sitemap|About US| Contact US: help@patsnap.com