Molding technology for hub supports
A molding process and wheel hub technology, applied in the field of automobile parts manufacturing, can solve the problems of large differences in comprehensive mechanical properties, complex shapes, and increase the difficulty of component production, and achieve the effect of improving shear strength and hardness, and improving comprehensive mechanical properties.
- Summary
- Abstract
- Description
- Claims
- Application Information
AI Technical Summary
Problems solved by technology
Method used
Image
Examples
Embodiment
[0018] A wheel hub bracket forming process, comprising the steps of:
[0019] (1) Blanking: choose cylindrical steel with a length-to-diameter ratio of (1.8-2.2): 1 as the forging raw material; the steel is made of 40Cr alloy steel;
[0020] (2) Forging: Heat the forging raw material to 1250±10°C, and then pull it out. After pulling out, the length increases by 20% to 30%, and then put it into the bending die for bending. The temperature of the bending die is 370±20°C, and the shape Initial forging: return the initial forging to the furnace and heat it to 1200±10°C, one end of the initial forging is the rod end, the other end is the head end, and the head end is chamfered according to the cross-sectional area of 1: (0.6~0.7):( 0.3~0.4) for forging, the head end is forged according to the ratio of 1: (0.9~1.1) to form a middle forging; the middle forging is returned to the furnace and heated to 1160±10°C, and then put into the forming mold for forming, the forming mold temper...
PUM
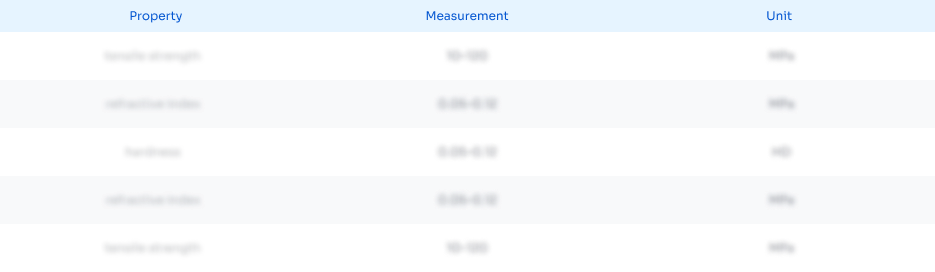
Abstract
Description
Claims
Application Information

- R&D Engineer
- R&D Manager
- IP Professional
- Industry Leading Data Capabilities
- Powerful AI technology
- Patent DNA Extraction
Browse by: Latest US Patents, China's latest patents, Technical Efficacy Thesaurus, Application Domain, Technology Topic, Popular Technical Reports.
© 2024 PatSnap. All rights reserved.Legal|Privacy policy|Modern Slavery Act Transparency Statement|Sitemap|About US| Contact US: help@patsnap.com