Recovery method for starch syrup ion exchange material pressing water
A starch syrup and recovery method technology, applied in chemical instruments and methods, sugar production, sugar production and other directions, can solve the problems of large equipment processing capacity, high operating pressure, membrane blockage, etc., and achieves low recovery cost and energy consumption. The effect of reducing and reducing the cost of refinement
- Summary
- Abstract
- Description
- Claims
- Application Information
AI Technical Summary
Problems solved by technology
Method used
Image
Examples
Embodiment 1
[0027] A method for recovering starch syrup separation press water, comprising steps as follows:
[0028] (1) After the normal use of the ion exchange column fails, use deionized water to press the material. The flow rate of the material is 3 times the volume of the resin per hour, and the sugar solution with a concentration of more than 15% is recovered to the pre-delivery tank for ion exchange again, and the collection concentration is 15%. The sugar liquid until 0 is sent to the temporary storage tank of dilute sugar water, waiting for subsequent processing.
[0029] (2) Carry out ultrafiltration membrane filtration with all press dilute sugar water collected in step (1), the molecular weight cut-off scope of ultrafiltration membrane is 7kDa, operating pressure 0.8Mpa, operating temperature≤45 ℃, concentration factor 6. With impurities such as proteins and pigments with a large molecular weight cutoff, the sugar is passed through, and the retained liquid is sent to the sewa...
Embodiment 2
[0033] A method for recovering starch syrup separation press water, comprising steps as follows:
[0034] (1) After the normal use of the ion exchange column fails, use deionized water to press the material. The flow rate of the material is 4 times the volume of the resin per hour. The sugar solution with a concentration of more than 15% is recovered to the pre-delivery tank for ion exchange again, and the collection concentration is 15%. The sugar liquid until 0 is sent to the temporary storage tank of dilute sugar water, waiting for subsequent processing.
[0035] (2) All the pressed material dilute sugar water collected in step (1) is subjected to ultrafiltration membrane filtration. The molecular weight cut-off range of the ultrafiltration membrane is 8kDa, the operating pressure is 0.9Mpa, the operating temperature is ≤45°C, and the concentration factor is 7. With impurities such as proteins and pigments with a large molecular weight cutoff, the sugar is passed through, a...
experiment example
[0041] The obtained starch syrup detachment and pressure water recovery method of Examples 1-2 was compared with the method of Comparative Example 1 in terms of processing capacity, energy consumption and detachment cost. The comparison results are shown in Table 1 below.
[0042] Table 1
[0043]
[0044] As can be seen from the above table 1, the method for recovering starch syrup separation pressure feed water of the present invention reclaims starch syrup separation pressure feed water, and the dilute sugar solution is refined and preliminarily concentrated by membrane equipment. The processing capacity of the present invention is Large size, high efficiency, low energy consumption, and low recovery cost; the water and sugar in the washing liquid of the separation column are recovered, reducing the washing water discharge and washing water COD; the sugar solution is recycled after concentration, and the dialyzed water can be recycled Repeated flushing of the separation ...
PUM
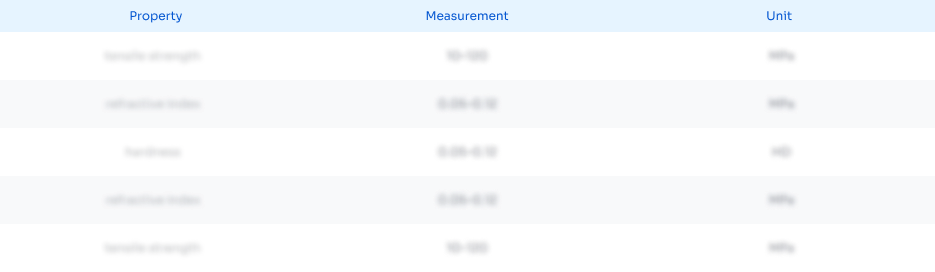
Abstract
Description
Claims
Application Information

- R&D Engineer
- R&D Manager
- IP Professional
- Industry Leading Data Capabilities
- Powerful AI technology
- Patent DNA Extraction
Browse by: Latest US Patents, China's latest patents, Technical Efficacy Thesaurus, Application Domain, Technology Topic, Popular Technical Reports.
© 2024 PatSnap. All rights reserved.Legal|Privacy policy|Modern Slavery Act Transparency Statement|Sitemap|About US| Contact US: help@patsnap.com