Grinding device for coating processing and operation method of grinding device
A grinding device and coating technology, applied in the field of coating processing, can solve the problems of difficult heat, uneven coating grinding quality, low grinding efficiency, etc., and achieve the effects of improving quality, improving grinding quality and improving work efficiency.
- Summary
- Abstract
- Description
- Claims
- Application Information
AI Technical Summary
Problems solved by technology
Method used
Image
Examples
Embodiment 1
[0020] as attached figure 1 Shown: a grinding device for paint processing, including grinding barrel 1, motor 2, transmission shaft 3, stirring rod 4, filter plate 5 and grinding beads 6, characterized in that: the grinding barrel 1 is set on the bracket 7, and the grinding bucket 1 is provided with a feed bin 8, a feed bin 9, a water inlet pipe 10, and a water outlet pipe 11. The grinding bucket 1 is provided with an interlayer 12, and the interlayer 12 is connected with the water inlet pipe 10 and the outlet pipe. The water pipe 11 is connected, the water inlet pipe 10 and the water outlet pipe 11 are provided with a valve 13, the discharge bin 9 is provided with a filter screen 14 and a regulating valve 15, and the motor 2 is arranged at the bottom of the grinding barrel 1 , the transmission shaft 3 is arranged in the grinding barrel 1, one end of the transmission shaft 3 is connected with the motor 2, and a connection block 16 is arranged on the transmission shaft 3, and t...
Embodiment 2
[0027] as attached figure 2 Shown: as attached figure 1 Shown: a grinding device for paint processing, including grinding bucket 1, motor 2, transmission shaft 3, stirring rod 4, filter plate 5, grinding beads 6 and grinding roller 18, characterized in that: the grinding bucket 1 is set on the bracket 7, and the grinding bucket 1 is provided with a feeding bin 8, a feeding bin 9, a water inlet pipe 10, and a water outlet pipe 11. The grinding bucket 1 is provided with an interlayer 12, and the interlayer 12 and the inlet The water pipe 10 and the water outlet pipe 11 are connected, the water inlet pipe 10 and the water outlet pipe 11 are all provided with a valve 13, the described discharge bin 9 is provided with a filter screen 14 and a regulating valve 15, and the described motor 2 is arranged on The bottom of the grinding bucket 1, the transmission shaft 3 is arranged in the grinding bucket 1, one end of the transmission shaft 3 is connected with the motor 2, and a connec...
PUM
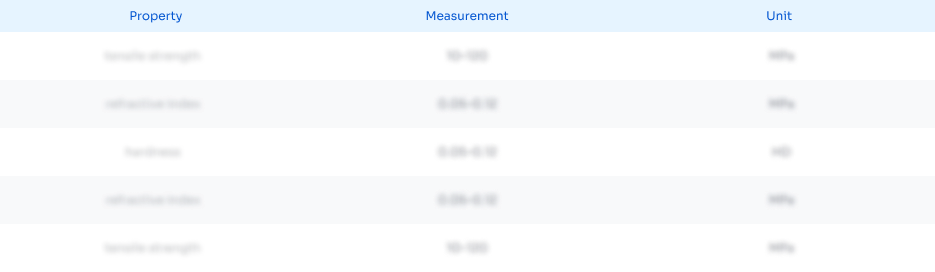
Abstract
Description
Claims
Application Information

- R&D
- Intellectual Property
- Life Sciences
- Materials
- Tech Scout
- Unparalleled Data Quality
- Higher Quality Content
- 60% Fewer Hallucinations
Browse by: Latest US Patents, China's latest patents, Technical Efficacy Thesaurus, Application Domain, Technology Topic, Popular Technical Reports.
© 2025 PatSnap. All rights reserved.Legal|Privacy policy|Modern Slavery Act Transparency Statement|Sitemap|About US| Contact US: help@patsnap.com